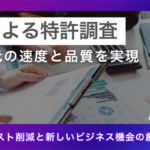
AI活用で特許調査はここまで進化する!品質・速度を異次元に
2025-07-25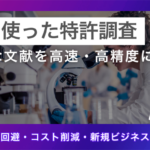
AI活用で特許調査はここまで進化する
2025-07-27技術の空洞化|背景・メリット・デメリットと企業対応策
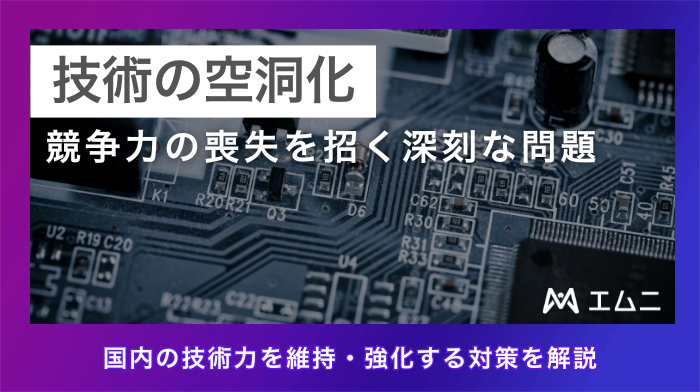
企業は、コスト削減や市場拡大を目的に、生産や開発の拠点を海外に移しています。その一方で、日本国内では技術や人材が育ちにくくなっているのが現状です。その結果、「技術の空洞化」という問題が深刻化しています。
このままでは、将来のものづくり力が失われ、企業の競争力そのものが弱まっていくかもしれません。
本記事では、この問題の原因や影響、そして今すぐ取り組むべき対策についてわかりやすく解説します。
技術の空洞化とは
技術の空洞化とは、工場や研究所を海外へ移すだけではなく、そこで培われるはずの設計ノウハウや試作の経験、熟練技術者の知見までが一緒に流出してしまう現象です。
例えば、自動車メーカーがエンジン開発拠点をタイに移した結果、国内では高出力エンジンの開発セクションが消滅し、新モデルの心臓部を設計できる人材が不足する。
そんな事態が「技術の空洞化」です。
参考文献:産業の空洞化は何が問題か?
産業の空洞化との違い
産業空洞化は主に「工場が海外へ移ったことで地元の雇用や街の商店街が元気を失う」といった形ある資産の移転を指します。
それに対して技術の空洞化は、工場という建物の移転を越えて、「設計部門や試験設備、その背後にある形のない技術力そのものが国外に移ってしまう」点に着目します。
もし家電メーカーの製造ラインが海外に移っても、国内に設計部門などが残っていれば新商品開発は続けられるでしょう。
しかし、これらの技術も一緒に流出すると、まるで職人の道具箱ごと持ち出されてしまい、その技術を再現できなくなるような状態になります。
産業空洞化が「工場の引っ越し」であるなら、技術の空洞化は「建物の中に詰まった大切なノウハウまで持ち去られる引っ越し」なのです。
参考文献:産業の空洞化は何が問題か?
技術の空洞化の原因と背景
技術の空洞化は、一つの原因だけで起こるものではありません。
世界の経済状況、企業のコスト削減策、そして国内の社会構造の変化など様々な要因が入り交じって進みます。
ここでは、技術の空洞化を招く代表的な3つの要因をわかりやすく解説し、なぜ今この問題が起きているのか、その背景にある構造的な課題まで丁寧に見ていきます。
コスト削減のための海外生産
技術の空洞化の一つの理由として挙げられるのが、コスト削減のために工場を海外に移す動きです。
企業は賃金の低い国に製造を委託することで、人件費を大幅に抑え、短期間で利益を上げようとしています。
たとえば、ドイツの製造業の約80%は「人件費削減」を海外移転の主な目的にしており、計算上は7〜9%のコスト削減が可能とされています。なので多くの企業が生産の拠点を人件費の安い海外に移していました。
しかし、その結果として、熟練作業者の手の動かし方、機械のわずかな異常を感知する勘、など現場で培われるはずの技能や改善のノウハウが国内に残らなくなり、技術の基盤が次第に弱まっていきます。
実際、OECDの調査では1980年代以降、衣料品や電子部品、機械部品などの産業で生産の海外移転が進んだ結果、先進国の製造現場の雇用が平均10〜20%も減少し、技能や現場力の流出が起きていることが報告されています。
引用元:Aggressive reshoring of supply chains risks significant GDP loss, warns OECD
さらに近年では、海外の工場が急に稼働を停止したり、品質に問題が出たりするリスクも高まり、再び国内での生産を検討する企業も増加中です。
ただし、英フィナンシャル・タイムズによると、急激に生産を国内に戻すと、経済全体に大きな負担がかかり、GDPが最大12%下がる恐れもあるとされています。
このように、目先のコスト削減にはつながっても、製造を安易に海外に任せ続けることは、結果的に国内の技術力を弱めてしまい、長い目で見れば日本の「ものづくり」の土台そのものを損なうリスクをはらんでいるのです。
参考記事:
- Offshoring, Reshoring, and the Evolving Geography of Jobs: A Scoping Paper
- Aggressive reshoring of supply chains risks significant GDP loss, warns OECD
為替の変動による影響
為替変動は、企業の生産・開発拠点の再配置を通じて、国内技術基盤の空洞化を招く一因となり得ます。
日本は戦後、1ドル=360円という固定相場制のもとで高度経済成長を遂げました。
この体制は、第二次世界大戦後に構築された「ブレトンウッズ体制」と呼ばれる国際的な為替制度に基づいており、各国の通貨を米ドルに固定し、米ドルを金に交換できる仕組みによって世界経済の安定が図られていました。
しかし、1971年にアメリカが金とドルの交換停止を宣言し、この体制は崩壊。以降、日本円は変動相場制へと移行し、市場の需給によって為替レートが決まる仕組みとなりました。
それ以降、円高(円の価値が上がる)と円安(円の価値が下がる)が周期的に繰り返されるようになります。
1985年には、アメリカの貿易赤字拡大を受け、主要5カ国(米・日・独・仏・英)が協調してドル安を進めることに合意した「プラザ合意」が結ばれました。
引用元:プラザ合意とは | OANDA FX/CFD Lab-education(オアンダ ラボ)
これにより急激な円高が進み、円は1985年9月の1ドル=240円台から、1995年半ばには88円以下にまで上昇しました。
この大幅な円高は、日本の輸出産業、特に自動車や電機といった製造業に大きな打撃を与え、多くの企業が為替リスクを回避するため、生産拠点の海外移転を加速させるきっかけとなりました。
こうした為替の変動による影響は、現在に至るまで続いています。
例えば10%の円高が機械輸出を約6%減少させるという分析があるように、企業は輸出採算の悪化を避けるため、海外移転を進めています。
一方で、円安局面では輸入原材料のコスト増加が企業収益を圧迫します。実際、81.5%の企業が「コストが増加する」と回答しており、為替リスクを抑えるために「現地生産・現地消費」モデルへの転換や、研究開発機能そのものを海外に移転する動きもみられます。
為替変動は、単に国家間での通貨の価値が変わるという事実にとどまりません。
この変動は企業の経営判断や戦略に直接影響を及ぼし、生産や研究開発の拠点選びにも波及します。さらには、国内の技術基盤や産業構造、ひいては国家レベルの競争力にも関わる重要な要素なのです。
参考文献:
- Japan’s Experiences under the Bretton Woods System: – Capital Cotrols and the Fixed Exchange Rate
- The impact of exchange rates on Japan’s machinery exports since 1990 | CEPR
- Survey Report on Overseas Business Operations by Japanese Manufacturing Companies
国内技術継承の不足
技術の空洞化が進行する背景には、技術継承の停滞という日本国内での要因も見逃すことはできません。
特に製造業の現場では、長年にわたり日本のものづくりを支えてきた団塊世代の熟練技術者が大量に退職期を迎えており、その結果として彼らが蓄えてきた技術の継承が深刻な課題となっております。
このような技術継承の困難さをさらに悪化させているのが、若手人材の不足と、技能伝承を支える育成基盤の脆弱さです。
少子化の影響も相まって、専門職や生産従事者の人手不足は年々深刻化しており、たとえば工業高校の求人倍率が20倍を超える例もあるなど、産業界の人材ニーズに対して教育現場が十分に応えきれていない状況が続いております。
また、博士号取得者数の伸び悩みや、研究者の賃金水準が国際的に見て相対的に低いことなども、若手人材の海外流出や研究職離れを引き起こす一因となっています。
加えて、日本企業における人材育成投資は諸外国と比べて低水準にとどまっており、OJTなどを通じた技能継承の機会も限定的です。
このような状況の中で、世代間の自然な知識や技能の伝達が途切れがちになり、熟練者から若手への技術の受け渡しが、制度的にも文化的にも難しくなっているのが現状です。
その結果、企業はまたベテラン人材に依存せざるを得ず、彼らの退職がそのまま企業の技術資産の喪失につながるという、構造的なリスクを抱えることになります。
これは単に人材が不足しているという問題にとどまらず、イノベーションの源泉ともいえる高度な知識と経験の蓄積が、社会全体で継承されにくくなっているという、より深刻な次元での空洞化であるといえます。
▼ 技能継承における課題や導入方法の全体像はこちら
技能伝承とは?問題点、解決策、導入方法について徹底解説
▼ 暗黙知の共有・形式知化の手法を知りたい方はこちら
生成AIで暗黙知を形式知化するメリットやプロセスを解説
▼ 製造業における技術継承の意義と取り組み事例について詳しくはこちら
技術継承|製造業の未来を支える知恵と技の伝承
参考記事:
技術の空洞化が招くリスク
技術の空洞化が進行すると、企業経営や国内産業、ひいては地域社会にまで、深刻なリスクをもたらします。
短期的なコストメリットの裏で、静かに、しかし確実に、日本の競争力の基盤が蝕まれていくのです。
この章では、技術の空洞化が具体的にどのような危険性をはらんでいるのかを明らかにします。
ノウハウの喪失
生産や開発の拠点が海外へと移されることで、日本国内では技術やノウハウが新たに育つ環境が失われつつあります。
「ものづくり」は、現場での試行錯誤と改善の積み重ねによって進化していくものです。しかし、生産の現場が国外に移れば、その機会が途絶えることになります。
経済産業研究所などの調査によれば、輸出する代わりとしての海外展開は、国内で蓄積された技術資産の海外移転を促し、それに伴って国内製造の縮小傾向を強めていることが明らかにされています。
とくに、労働集約的かつ低技術な工程や旧型製品の生産が移転対象となる傾向が強く、国内では現場知の蓄積が難しくなっているのが現状です。
このような構造変化により、熟練技術者の引退とともにノウハウ継承が断たれ、企業の「宝」とされてきた技能が失われつつあるのです。地方の製造拠点で培われた技術も風化の危機にさらされ、地域経済や技術基盤の弱体化が懸念されるでしょう。
実際、アジア向けの輸出代替型投資だけでも、国内雇用が58万人分(これは鹿児島市の人口に匹敵する規模)減少したとされており、その多くは技能の蓄積の場であった部門です。グローバル展開によるメリットがある一方で、国内で技術を育て、伝える土壌がやせ細っている現状は見過ごせません。
この現象は、枝が海外に伸びて果実を実らせる一方で、国内の幹や根が衰え、新しい芽が出ず古い葉が落ちていく木のようなものです。幹が弱れば、木全体、すなわち日本の技術力そのものが危機に瀕すると言えるでしょう。
▼ 熟練工の技能を次世代につなげる方法はこちら
熟練工の技能伝承を成功させるには|生成AIの恩恵
参考記事:
トラブル対応力の低下
製造や開発を外部企業に委託するアウトソーシングは、経営の効率化に寄与する有効な手段です。
しかし、それが行き過ぎてしまうと、自社内にものづくりの実態を理解する人材が育たなくなり、技術の中核を外部に委ねたままの状態に陥ります。
本来、製品に不具合やトラブルが生じた際には、現場で原因を素早く特定し、自らの手で根本的な対策を講じる力が求められます。
ところが、設計や製造の詳細を把握しているのが外注先のみとなれば、マニュアルにない異常事態への対応は著しく困難になるでしょう。
このような構造の変化は、ただ品質を損ねるというだけでなく、企業の危機対応力そのものを蝕みます。現場に技術がない、ノウハウが残っていない、試作や検証の場もないという状態では、異常の兆候を察知することも、対処法を試行錯誤することもできません。
その結果、突発的な製品不良や市場クレームが致命的なダメージとなり、企業の信頼や持続性を大きく揺るがす事態へとつながるのです。
参考記事:
地域産業・雇用への悪影響
企業の工場や事業所は、地域にとって単なる雇用の場ではなく、経済と社会を支える中核的な存在です。
しかし、こうした拠点が海外へ移転・閉鎖されることで、そこで働いていた従業員が職を失うだけにとどまらず、関連する下請け企業や周辺のサービス業にも深刻な影響が及びます。影響は限定的ではなく、地域経済全体の基盤を揺るがす事態へとつながっていきます。
このような変化は、企業単体の経営判断に収まらず、地域全体の自立性や持続力を損なう構造的な問題といえるでしょう。
とくに中小企業への影響は大きく、調査によると66.6%の企業が受注単価や販売価格の下落を、38.4%が取引先の海外移転による売上減少を経験したとされています。多くの中小企業は、技術体系の基盤を支える役割を担っており、その衰退は技術集積の断絶に直結するのです。
一度失われた基盤技術は、短期間で再構築するのが難しく、産業全体の力が目に見えない形でじわじわと静かに弱まっていくと考えられます。
とくに製造業の空洞化が進んだ地域では、公共投資による地域再生策も十分な効果を発揮できておらず、地域の活力を取り戻すのは容易ではありません。
こうした状況が長引けば、地域経済だけでなく、より広い地域産業、雇用全体にも深刻な影響が及ぶおそれがあります。
参考記事:
技術の空洞化が進行した事例
技術の空洞化は、決して抽象的な概念ではありません。すでに日本の様々な産業分野で、その兆候や深刻な影響が現実のものとなっています。
ここでは、具体的な事例を通じて、技術の空洞化がどのように進行し、どのような結果を招くのかを多角的に検証します。
日本製造業における工場海外移転
1980年代後半の円高を契機に、日本の製造業は生産コストの抑制と市場競争力の強化を目的として、アジア諸国を中心に海外への工場移転を急速に進めました。
特に自動車や電機といった基幹産業ではこの動きが顕著であり、それに連なる部品・素材産業も次々と海外展開に踏み切ったのです。
その結果、国内における生産能力は相対的に低下し、多くの現場知や技術の蓄積機会が国内から失われることになりました。
実際に、2024年版ものづくり白書によると、日系大手製造業ではこの20年で海外売上比率が急増し、現在では売上の過半数が海外で構成されています。
従業員構成においても、連結ベースで6割以上が海外現地法人に所属しており、製造業の中心が国内から海外へ移った構造変化が明確に表れています。さらに、円高を背景としたM&Aや現地法人設立を通じて、グローバル事業の規模は拡大を続けてきました。
一方で、グローバルに広がった製造網を統合的に管理する仕組みは不十分であり、企業グループ全体が「連邦経営」と呼ばれる分断状態にあることが指摘されています。
海外現法が独自に運営される一方で、本社からのガバナンスが弱く、ヒト・モノ・カネ・データといった経営資源を横断的に活用できていない状態です。この分断は、企業の「稼ぐ力」を制約し、国内外をまたいだ技術継承やノウハウの活用を困難にしています。
海外展開によって製造業の外延は拡大しましたが、その過程で国内のものづくり基盤の弱体化と企業統治の緩さが生まれました。
この構造は、個々の拠点は航行しているものの、船団全体としては統率を欠き、最大限の力を発揮できていない日本の製造業の現状を象徴しています。今必要なのは、分散した力を束ね、全体としての競争力を取り戻すための舵取りです。
参考記事:2024年版 ものづくり白書 概 要
IT・内製化不足によるスキル失陥事例
日本企業におけるITの内製化不足は、ものづくりと同様に深刻なスキルの空洞化を引き起こしています。
システムの開発や運用を外部のITベンダーに依存する体制が長年続いた結果、自社内にITに関する専門知識や技術を持つ人材が育たず、システムの企画・設計能力や障害時の即応力が著しく低下しています。
業務現場の課題を理解したうえで自らシステムを改善・進化させる能力が失われ、最新のデジタル技術を活用して事業を変革するいわゆる「DX」を推進するための基盤が欠けているのです。
情報処理推進機構の調査では、DXを担うべき「ビジネスアーキテクト」や「データサイエンティスト」といった人材が大きく不足しており、企業の多くが「どのような人材を必要とするのかさえ定義できていない」という段階にとどまっています。
またガートナーの調査でも、13種類の主要IT人材のうち全てが不足していると回答した企業は8割以上に達し、特に約4割の企業ではそれぞれが「大いに不足」しているという深刻な実態が明らかになっています。
引用元:gartner 調査結果
この人材不足は新しい技術領域だけに限らず、基幹系システムのような旧来のIT領域にも及んでおり、企業の基盤を支える重要な知識・技能すら維持できない状況です。
さらに、IT人材の獲得に向けたブランディングや処遇の工夫も進んでおらず、「何をすれば良いのか分からない」という企業側の認識不足が問題を構造的に固定化しています。
以上のように、日本企業はITの内製力を欠いたまま外部依存を深めた結果、DXを推進するために必要な人材・スキル・組織基盤の多くを失いつつあります。
今後の競争力を維持・強化するためには、IT人材の育成と確保を中長期的な戦略の中心に据え、内製化を含む自律的な技術体制の構築が急務といえるでしょう。
▼ 製造業のDX導入における課題と具体的なステップはこちら
製造業のDXとは?メリット・ロードマップ・事例を徹底解説
参考記事:
小売業での店舗空洞化との類比
技術の空洞化と構造的に似た現象として、小売業における中心市街地の店舗空洞化が挙げられます。かつて地域の生活や文化の拠点であった商店街は、郊外の大型ショッピングセンターの台頭やインターネット通販の普及によって客足を奪われ、空き店舗の増加とともにその賑わいを失っていきました。
総務省や経済産業省の調査でも、モータリゼーションの進展や公共施設の郊外移転、少子高齢化や人口減少などが複合的に影響し、中心市街地の商業機能や集客力が著しく低下していることが示されています。
地方百貨店の閉店や、労働人口の減少、空き地や空き家の拡大といった具体的な症状が確認され、都市の構造そのものがまるでスポンジのようにスカスカになっていく現象として問題視されています。
この空洞化の本質は、地域の中心であった場所が、周囲の環境や人々のニーズの変化に対応できず、本来担っていた役割を果たせなくなったことにあります。顧客に求められる機能や利便性を提供できなければ、人はより便利で快適な場所へと移動し、結果として旧来の商店街は存在意義を失っていきます。
企業の技術空洞化も同じ構造を持っています。ものづくりの中核を外部に依存し、自社内での開発力や技術的判断力を育てられなくなれば、市場や顧客の変化に対応する力を失ってしまいます。
技術という企業の競争力の根源が失われれば、提供できる価値そのものが揺らぎ、企業の持続的な成長は難しくなります。
つまり、店舗空洞化と技術空洞化はいずれも、自らが持っていた中心的な機能を自らの手で支えきれなくなったときに起こる現象です。
活気を失いシャッターが閉まる街と、技術の蓄積が途絶え競争力を喪失していく企業。その背景には、変化への対応力と、価値の源泉を手放してしまったという共通の課題が横たわっています。
参考記事:
技術の空洞化を防ぐ企業の対応策
深刻なリスクをはらむ技術の空洞化ですが、手をこまねいていれば、企業の、そして日本の未来は拓けません。
この流れに抗い、持続的な成長を確保するためには、企業自身が主体的に行動を起こすことが不可欠です。
ここでは、技術の空洞化を防ぐために企業が取り組むべき3つの具体的な対応策を提案します。
コア技術の内製化と人材育成
企業がすべての技術を自社で持つ必要はありませんが、競争力の源となる「コア技術」だけは安易に外部に任せるべきではありません。
特に製造業では、設計や調達、物流、営業などと製造部門を連携させ、情報を一元管理しながら、技術を社内に蓄積・活用する体制づくりが重要です。これは単なる効率化ではなく、新しい価値を生む基盤となります。
この内製化を支えるのが人材育成です。デジタル人材は世界的に不足しており、外部からの採用に頼るだけでは限界があります。ダイキン工業のように、自社で2年間専門教育を施し、実務とデジタルの両方を理解した「π型人材」を育てる取り組みが注目されています。
引用元:通常業務を2年間免除、ダイキンは企業内大学で「Π型人材」を徹底育成
こうした人材が、熟練の現場知識を活かしてAIを導入するなど、スピードと実効性のある技術革新を可能にしています。
また、若手が挑戦し成長できる環境づくりも欠かせません。
能力に応じた評価や配置、昇進を通じて、学びがキャリアに結びつく仕組みが育成の効果を高めます。中小企業でも、研修と実務を通じて短期間でリーダーに育つ例があり、人材育成が企業全体の活力につながっています。
コア技術の内製化と、それを担う人材の戦略的な育成は、企業の未来を切り拓く鍵です。
自社の強みを自らの手で磨き続ける力こそが、変化の時代を生き抜く本当の競争力となります。
▼ 製造業における人手不足の実態と対応策についてはこちら
製造業の人手不足|浮き彫りになる問題とその解決策
▼ 若年層の製造業離れに対する対策を知りたい方はこちら
製造業の若者離れ|原因や効果的な対策を解説
参考文献:
オープンイノベーションと技術提携
自社にない技術やアイデアを外部から取り入れ、新たな価値を創出する「オープンイノベーション」は、自前主義の限界を突破し、変化の激しい市場環境に柔軟に対応するための有効な戦略です。
単なる業務委託とは異なり、自社が主体となって外部と協働することで、スピード感のある開発と革新的な成果が期待されます。
たとえば、ベトナムの大手IT企業FPT ISでは、スタートアップ企業を買収し、その技術や人材を自社文化に融合させることで、アイデア創出力と組織の柔軟性の向上を実現しています。
同様に、日本の花王や資生堂、JALなども、大学発ベンチャーや異業種スタートアップと連携し、製品やサービスの共同開発に取り組んでいるところです。
このような事例では、開発期間の短縮に加え、自社内では生まれにくい着想がビジネスとして具体化されるという点で、大きな意義があるといえるでしょう。
また、オープンイノベーションは社内人材にも強い刺激を与えます。外部との協業によって、新しい発想や技術に触れる機会が増え、社員の創造性や挑戦意欲が引き出されるからです。
CMCやG-Groupのように、大学や研究機関と連携して若手技術者を育てる企業も増えており、社内外の知の融合が成長の起点になっています。
イノベーションの担い手が、必ずしも企業の内部にいるとは限りません。むしろ、外部のスタートアップや研究機関と手を組むことで、自社の強みを再定義し、新しい市場や顧客体験を創り出すことが可能になります。
オープンイノベーションは、企業の組織力と創造力をともに引き上げる、攻めの成長戦略なのです。
参考記事:
地域・国の支援策活用(補助金・連携拠点)
技術の継承や設備投資は、企業にとって大きな資金的負担となり得ます。
そこで、国が提供する補助金制度を活用することで、その負担を軽減し、成長の加速につなげることが可能です。
たとえば「事業承継・M&A補助金」は、親族内や従業員への承継、あるいはM&Aを通じた事業再編に対して、最大1,000万円の設備投資支援を行い、必要に応じてPMI(経営統合)費用や廃業支援費も最大150万円まで補助します。
M&Aに関する専門家の活用費用には、一般的な上限として600万円から800万円の補助が認められており、特定の条件(100億企業要件)を満たす場合は上限2,000万円の補助が認められます。
また、研究開発や設備投資に対しては「ものづくり補助金」があり、革新的な新製品・新サービスの開発、海外展開、そして付加価値の高いものづくりに対して、最大4,000万円までの補助を受けることが可能です。
補助率は中小企業で1/2、小規模事業者では2/3に設定されており、一定の賃上げに取り組む場合には上限の引き上げや補助率の加算も受けられます。こうした制度は、単なる資金援助にとどまらず、長期的な事業計画の策定や収益性の向上といった企業の成長戦略そのものを支援する設計になっています。
制度の活用には、電子申請や事前アカウント登録など一定の準備が必要ですが、それを上回るメリットが確実に存在します。
補助金は、言わば企業の航海におけるタグボートのような存在です。自力で進むには重すぎる船(設備や技術投資)も、補助という外部の推進力を借りることで、安全かつスピーディに目的地へと進むことができるのです。
挑戦への意欲と実行力さえあれば、これらの支援策は企業の未来を切り拓く強力な後押しとなるでしょう。
参考記事:
- 中小企業生産性革命推進事業「事業承継・M&A補助金」(十二次公募)の公募要領を公表します
- ものづくり・商業・サービス生産性向上促進補助金の第19回公募要領を公開しました | 中小企業庁
- 補助金 ものづくり
企業が今すぐ実践すべきアクション
技術の空洞化という大きな課題に対し、どこから手をつければよいのか分からないと感じる経営者も多いかもしれません。しかし、行動を起こさなければ何も変わりません。
ここでは、企業が技術力を再強化するために、今すぐ具体的に着手できる3つのアクションプランを提示します。
現状分析とKPI設定(技術者数・特許件数など)
自社の技術力を高めるうえで最初に行うべきは、現状を客観的かつ定量的に把握することです。
自社の強みとなるコア技術がどの分野にあり、どの領域が相対的に弱いのか、技術者の年齢構成やスキルの偏在状況、育成体制などを正確に把握しなければ、次の一手を誤るかもしれません。
たとえば、DXに取り組む企業の約8割が「人材・スキルの不足」を主要課題として挙げており(79.9%、2023年調査)、特にデータサイエンティストやソフトウェアエンジニアなどの中核人材は、5割以上の企業で「人員・スキルともに不足している」と報告されています。
こうした現状分析に基づき、「若手技術者の比率を3年で10%向上させる」など、明確なKPIを設定することが求められます。
実際、DXを推進できている企業では、「全社としてKPIが設定され、DX推進状況を評価している」とする回答が51.4%にのぼっており、KPIが推進力になっていることが明らかです。
自社の人材戦略を「採用」「リスキリング」「社内定着率向上」などに分解し、それぞれに指標を設けて定期的にモニタリングする体制が必要です。
また、KPIは社内向けの管理指標にとどまらず、外部のステークホルダーに対しても企業の進化を示す材料になります。企業価値向上を図る観点からも、技術人材に関する数値目標は、財務指標や成長戦略と結び付いた説得力のあるメッセージとなります。
一方、「特許出願件数を年間5件以上にする」といった数値目標については、調査資料から直接的な裏付けは得られていないものの、知的財産を定量的に管理する意識そのものは、研究開発力や技術成果の評価指標として今後さらに重要性を増すでしょう。
技術と人材という両輪の現状を把握し、進むべき方向と成果の物差しを明確にしておくこと。それにより組織全体の推進力と軌道修正力を確実に高めてくれます。
▼ 参入障壁を築くための特許戦略はこちら
企業価値を創る知財戦略|特許ポートフォリオの構築・分析・活用
参考記事:
拠点の再設置・技術継承プログラム導入
現状分析と目標設定が整ったら、次にすべきは実行段階への移行です。
その中でも急務となっているのが、ベテラン技術者の持つ暗黙知を形式知へと転換し、若手世代へ計画的に継承する仕組み、いわば「技術継承プログラム」の整備です。実際、製造業では59.5%の企業が技術継承に課題を抱えており、全産業平均(41.2%)を大きく上回る水準にあります。
団塊世代の大量退職が進む中で、熟練者が持つ貴重な知見をいかに共有資産として残していくかが、大きな課題となっています。
その継承には、単なる紙のマニュアルでは対応しきれない場面も多く、限界があると言えるでしょう。
こうした課題に対し、図面データをクラウド上で一元管理できる「CADDi Drawer」を導入した企業では、これまでベテランしか使いこなせなかった検索や判断のノウハウを、若手社員でも扱える仕組みに変換しました。
その結果、勉強会の開催や自発的な学びが活発化し、業務の属人化解消にもつながっています。
また、マニュアル動画の作成やAIチャットボットの導入により、指導の効率が高まり、OJTの負担が軽減されると同時に、若手が安心して質問できる環境も整いつつあります。
ある企業では設計ノウハウや過去のヒヤリハット事例をテキスト化し、AIの対話機能を通じて活用することで、技術情報の「見える化」と即時アクセスを実現しています。
加えて、技術の背景にある判断基準や勘所を伝えるには、人と人との接点も欠かせません。少人数のグループ活動や作業後の振り返りを通じて、ベテランが自らの経験を語り、若手がそこから学ぶ場を継続的に持つことが重要です。
こうした取り組みは、制度としての「メンター制度」にも近い機能を果たし、若手が積極的に提案し、質問できる心理的安全性のある職場文化の醸成にもつながります。
さらに拠点の国内再設置は、製造現場のノウハウを再構築するうえで重要な選択肢となります。その際には、「どこで、誰が、どのように技術を持つか」といった地理的・組織的な配置をあらためて見直すことが求められます。
技術継承を進めるための場の設計は、単なる制度設計だけでなく、拠点そのものの構造改革とも関わってくるでしょう。
技術継承プログラムとは、単に過去の知識を引き継ぐことではありません。それは、経験を資産化し、若手の学びを支える土台を築き、組織全体の競争力を次世代へとつなぐための仕組みなのです。
▼ 暗黙知の形式知化を進めたい方はこちら
形式知とは?暗黙知との違い、メリット、形式知化の手法を詳細に解説
参考記事:
- 中小製造業におけるAI活用×技術伝承事例:株式会社シンワバネスに学ぶ若手育成術
- AI活用で日本の製造業に迫り来る「技術継承問題」を克服! | NEC
- 技術継承とは?課題や解決方法、取り組み事例を紹介|製造業AIデータプラットフォームCADDi
定期レビューとPDCAによる技術体制の強化
技術体制の整備は、計画して終わりではなく、成果を定期的に検証し、必要に応じて見直しや強化を図ることが求められます。PDCAサイクル(Plan-Do-Check-Action)を継続的に回すことが、変化の激しい市場環境で技術的な優位を保つうえで欠かせません。
たとえばCTCグループでは、2021〜2023年度の中期経営計画において施策ごとにKPIを設定し、達成状況を定量的に評価してきました。未達成項目にも改善を重ね、PDCAの定着を図っています。2024〜2026年度の新たな中期計画でも、この姿勢を継続する方針です。
同社はまた、エンジニアのスキルを約2,000項目に分類・可視化した「エンジニアスキルインベントリ」を活用し、技術体制の実態把握や人材戦略に反映させています。さらに、社員が自ら学びを深められるよう、選択式研修やオンライン学習環境を整備し、人的資本の強化にも取り組んでいます。
AIや生成系技術の導入もPDCAの一部として位置づけられており、生成AIやAI検索エンジンの活用によって、生産性や成果物の品質向上が図られています。これは、Do(実行)とCheck(検証)のサイクルを加速させる好例です。
旭化成グループでも、重大リスクやサイバーセキュリティへの対応がPDCAの枠組みに基づいて監督されており、定期的な経営監査によって柔軟かつ継続的な対応が実現されています。
このように、PDCAを軸とした技術体制の強化は、環境変化への対応と内部資源の最適化を両立する有効な手段です。
重要なのは、最初から完璧な計画を立てることではなく、状況の変化に応じて柔軟に見直し、行動し続ける力です。技術の高度化や人材の多様化が進むいま、体制を更新し続ける姿勢こそが、持続的成長の土台となります。
▼ PDCAサイクルとAIを活用した戦略強化についてはこちら
「AI x データ分析」で経営戦略の精度を向上・経験と勘からの脱却
参考文献:
まとめ
技術の空洞化は、グローバル化の進展と国内の構造的な問題が絡み合って生じる、根深い課題です。生産拠点の海外移転は、短期的にはコスト削減というメリットをもたらすかもしれませんが、長期的には国内の技術基盤を蝕み、企業の競争力そのものを失わせるリスクをはらんでいます。
この課題を克服するためには、企業が自社の競争力の源泉であるコア技術の重要性を再認識し、それを守り育てるための内製化や人材育成に本気で取り組むことが不可欠です。
同時に、オープンイノベーションを通じて外部の知見を積極的に活用し、国や地域の支援策も最大限に利用する、しなやかで戦略的な経営が求められます。
自社の技術力を客観的に分析し、具体的な目標を掲げ、計画的に技術継承を進める。そして、その取り組みを継続的に見直し、改善していく。
こうした地道な努力の積み重ねこそが、技術の空洞化という大きな流れに抗い、企業の、そして日本のものづくりの未来を切り拓く唯一の道と言えるでしょう。
エムニへの無料相談のご案内
エムニでは、製造業をはじめとする多様な業種に向けてAI導入の支援を行っており、企業様のニーズに合わせて無料相談を実施しています。
これまでに、住友電気工業株式会社、DENSO、東京ガス、太陽誘電、RESONAC、dynabook、エステー株式会社、大東建託株式会社など、さまざまな企業との取引実績があります。
AI導入の概要から具体的な導入事例、取引先の事例まで、疑問や不安をお持ちの方はぜひお気軽にご相談ください。
引用元:株式会社エムニ