
製造業の若者離れ|原因や効果的な対策を解説
2025-05-21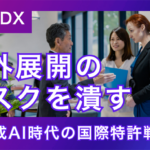
国際特許検索とは|海外展開の失敗を防ぐ生成AI時代の調査戦略
2025-05-24製造業のデジタル化|メリットやロードマップを詳しく解説
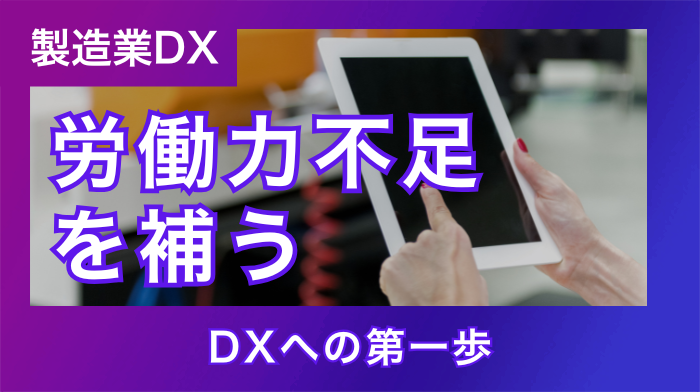
人材不足やコスト問題が深刻化するなか、製造業におけるデジタル化の推進は、今や無視できない経営課題となっています。
労働力の確保が難しくなる一方で、海外では生産性と柔軟性を両立する競合が次々と登場しています。デジタル化を先送りにすることは、市場競争力を自ら手放す行為にほかなりません。
本記事では、こうした危機を乗り越えるための課題整理から導入ステップ、成功事例までを段階的に解説していきます。
製造業のデジタル化とは
製造現場では今、紙の指示書や口頭での引き継ぎといったアナログな運用を見直し、あらゆる情報をデータとして蓄積・活用していく動きが進んでいます。まずは製造業における「デジタル化」とは何を指すのか、その基本的な枠組みを確認しておきましょう。
デジタル化とDXの違い
製造業における「デジタル化」と「DX(デジタルトランスフォーメーション)」は、しばしば混同されがちな概念です。しかし、その目的と対象範囲には明確な違いがあります。
まずデジタル化とは、紙媒体や口頭に依存していた現場情報をデータ化し、リアルタイムで把握・分析できるようにする取り組みを指します。例えば、紙の工程管理表をタブレットに置き換えたり、手書きの報告書をクラウド上のフォームに変更したりといった、現場レベルの改善が主な対象です。
一方でDXとは、単なる業務改善にとどまりません。ビジネスモデルそのものを再設計し、新たな収益源や競争優位性を創出するための変革プロセスです。現場のデジタル化を起点に、組織や戦略全体を変えていく中長期的な取り組みとも言えるでしょう。
両者の違いを区別せずに取り組むと、投資規模やKPI(重要業績評価指標)の設定を誤り、導入の初期段階で行き詰まるリスクがあります。まずはデジタル化を着実に完結させることが、DXの土台となるのです。
製造業におけるデジタル化
製造業におけるデジタル化とは、単に紙を電子化するだけでなく、現場で発生する情報をリアルタイムに把握・共有・分析できるようにすることを指します。こうした取り組みにより、生産効率の向上や品質トラブルの予防、属人化の解消など、さまざまな経営課題の改善が期待できます。
例えば、工程管理を紙のスケジュール表からタブレットに切り替えることで、現場ごとの進捗が即座に共有され、段取りミスや記録漏れの防止につながります。また、設備の異常音や温度変化をセンサーで検知し、自動でアラートを出す仕組みを導入すれば、故障や不良の兆候を早期に把握し、トラブルを未然に防ぐことも可能になります。
このように、現場に眠る情報をどう活かすかは、製造業のデジタル化において欠かせない視点です。
なぜ今、デジタル化が必要なのか
経済産業省は、老朽化した基幹システムをこのまま使い続けた場合に生じる莫大な経済損失を「2025年の崖」と名付け、強い危機感を示しています。システムのブラックボックス化によって保守費用が高騰し、年間で最大12兆円の損失が発生するとされています。
出典:経済産業省「DXレポート」(2018年)https://www.meti.go.jp/shingikai/mono_info_service/digital_transformation/20180907_report.html
現に、国内の製造業の約6割がレガシーシステムの維持に多くのコストを割かれ、本来は成長投資に回すべき資源を確保できない状態に陥っています。また、単純な業務効率化やペーパーレス化といった初期的な改善は、すでに多くの企業で一通り完了しており、それだけでは競争優位を築くには不十分になりつつあります。
また市場環境や顧客ニーズが激しく変化するなかでより柔軟で持続的な経営を実現するには、情報の見える化を起点としたデジタル化によって、組織全体の構造そのものを見直す必要があるといえます。
今やデジタル化は、単なるIT化ではなく、企業としての存続力を左右する重要な経営判断となっているのです。
『攻め』としてのデジタル化
「2025年の崖」が象徴するように、いま製造業は大きな転換点に立たされています。たしかに、レガシーシステムの刷新や現場データの活用基盤を整えるには一定の負担が伴いますが、それを機に収益性の改善や業務変革を実現する企業も少なくありません。
事実、経済産業省の調査によれば、デジタル化に取り組んだ中小企業の約30%が「売上高営業利益率が向上した」と回答しています。大規模な投資と見なされがちなデジタル化ですが、実際には業務の可視化や判断の高速化によって、経営面でのリターンが着実に得られることが示されています。
出典:中小企業白書(2021年)
https://www.chusho.meti.go.jp/pamflet/hakusyo/2021/chusho/b2_2_1.html?utm_source=chatgpt.com
こうした取り組みは、単なる『守り』ではなく、将来の競争力を見据えた『攻め』の投資として捉えることが重要です。
デジタル化がもたらす5つのメリット
デジタル化は、現場の効率化にとどまらず、経営全体のパフォーマンスを底上げする可能性を秘めています。本章では、生産性・品質・トレーサビリティ・開発設計・技能継承という5つの視点から、製造業における具体的な効果を見ていきます。
生産性向上とコスト削減
製造業におけるデジタル化の代表的な成果のひとつが、生産性の向上です。IoTセンサーと製造実行システム(MES)を連携させることで、ライン全体の稼働状況をリアルタイムに把握できるようになり、設備のムダや停止時間を可視化できます。
例えば、日本特殊陶業ではNECとの協業によりIoT基盤とダッシュボードを導入し、総合設備稼働率を5%向上させた実績があります。これによって、現場では停止原因の分析と改善サイクルが定着し、限られたリソースでもより高い生産効率を実現できるようになりました。
同様に、広島県の中小精密板金企業では、紙の指示書を完全に廃止し、クラウド型の生産管理システムに移行した結果、部材探索にかかる時間を80%削減しました。年間1万2千時間の工数削減を達成しています。紙依存を脱却するだけでも、コストと人手の両面で大きな成果を上げられることを示す好例です。
こうした取り組みにより、投資回収期間を1年半以内に短縮する企業も増えており、特に中堅規模の製造業にとっては、限られた資金を有効に活用するうえで現実的かつ効果的な施策となっています。
品質の向上と均一化
デジタル化によって工程内のデータを継続的に取得・分析することで、品質のばらつきや異常傾向を早期に発見しやすくなり、不良の発生を未然に防げるようになります。
例えば、過去の品質データとリアルタイムの計測値を照合することで、異常の兆候を事前に検知し、自動で対処フローを起動する仕組みを構築している企業もあります。人手による目視や経験則に頼っていた品質管理が、再現性と即応性の高い体制へと移行していくのです。
先ほども紹介した日本特殊陶業では、IoTとリアルタイム解析を組み合わせることで、設備単位の不良要因を把握し、歩留まりを30%改善。年間数十億円規模の原材料ロス削減につながっています。このように品質改善の取り組みは、収益インパクトにも直結します。
また品質トラブルはリコールやクレーム対応といった後工程に大きな負担を生じさせます。工程段階で早期に対応できれば、こうした影響を最小限に抑えられるため、デジタル化による品質管理の強化は全体最適の観点でも重要です。
トレーサビリティの強化
製造工程におけるトレーサビリティの確保は、品質問題の迅速な原因究明と影響範囲の特定に欠かせません。デジタル化によって、製品や部品の製造履歴をロット単位で自動的に記録・追跡できるようになれば、対応スピードと精度は格段に向上します。
例えばオムロン草津工場では、画像解析とセンサーを活用した自動検査工程を導入することで、ヒューマンエラーによる見逃しをなくし、不良流出のゼロを実現しています。また、リコー沼津事業所ではRFIDを用いた製造管理システムを構築し、部品や製品の履歴をリアルタイムで把握できる体制を整備しました。
こうした仕組みにより、仮に問題が発生した場合でも対象範囲を正確に特定でき、回収コストの低減やブランド毀損リスクの最小化が可能になります。トレーサビリティは今や、企業の信頼性や市場対応力を支える基盤として、その重要性を一層増しています。
開発・設計の高度化
製品のライフサイクルが短期化し顧客ニーズも多様化するなかで、開発・設計にはこれまで以上のスピードと柔軟性が求められています。こうした背景から、設計段階でのデジタル活用が競争力の源泉となりつつあります。
例えば、製品の3Dモデルと実際のセンサーデータを連携させたデジタルツインを活用すれば、試作前の段階で各種条件下の動作や不具合リスクをシミュレーションできます。これにより、実機での試作回数や修正工数が大幅に削減され、開発スピードと品質の両立が可能になります。
さらに、設計・製造部門間での情報連携がスムーズになることで、図面の意図が正確に現場へ伝わり、後工程での手戻りややり直しといったロスも抑えられます。
三菱電機では、生産ラインの設計にデジタルツインを応用し、ライン立ち上げ後の調整時間を50%、稼働率を10ポイント向上させた事例も報告されています。開発段階から現場の条件を反映させることで、試作・調整にかかるコストを根本から削減できます。
こうした設計と現場の一体化は、今後のものづくりにおいて不可欠な体制と言っても過言ではありません。
技能伝承と人材不足対策
デジタル技術は熟練技能の継承と共有を支え、若手の定着を促す仕組みづくりにも貢献します。
熟練者のノウハウをARとAIで可視化し、作業ガイドとして現場へ配信した企業では、習熟期間を三分の一に短縮しました。若手でもベテラン並みの作業精度を早期に獲得できるため、人員構成の高齢化を補うことができます。
導入ステップとロードマップ
デジタル化は、やみくもにツールを導入するだけでは成果につながりません。現場の課題に即した目的を定め、段階的に進めることこそが成功の鍵です。まずは小さな改善から始めて、全体展開につなげるステップ設計が重要になります。ここでは、効果的な導入を実現する3つのステップを紹介します。
現状課題の可視化とKPI設定
最初のステップは、現場で何が課題なのかを定量的に捉えることです。
工程別の滞留時間、設備稼働率、不良率といった指標を5〜7項目程度に絞り、数値として可視化することで、改善すべきポイントが明確になります。
あわせて、現状を評価するための**KPI(重要業績評価指標)**を定義し、月次などの定期サイクルでギャップを分析します。改善効果の可視化は、現場の納得感を高め、投資対効果の説明根拠にもなります。
「測定できないものは改善できない」という原則を徹底することが、デジタル化を成功に導く第一歩となります。
IoT・ロボットなど適用技術の選定
課題が可視化できたら、次はそれを解決するための最適な技術を選定します。重要なのは「何が使えるか」ではなく、「何を解決すべきか」から逆算することです。
例えば、加工時間にばらつきがある工程に対しては、いきなり協働ロボットを導入するのではなく、まずNC機の稼働ログを取得して原因を分析したほうが、費用対効果が高くなる場合もあります。
技術選定は、現場で起きている現象の因果関係を把握したうえで、最小限の投資で最大の効果を出すという観点から行うべきです。現場目線と経営目線のバランスが問われる工程とも言えるでしょう。
PoCから全社展開までのフェーズ管理
技術の有効性が見込まれたら、まずは小規模なPoC(概念実証)から始めるのが定石です。例えば1ライン、1工程など限定的な範囲で試験導入し、3か月以内にROI(投資対効果)を検証します。
この段階で期待値を下回る場合は、原因を特定し再設計を行います。PoC段階でROIが15%未満のケースでは、本格展開を見送る判断をする企業も少なくありません。
成功の目安として、投資回収期間を2年以内に設定する企業が多数派です。PoC → 段階展開 → 全社展開というステップを踏むことで、スピードと安全性のバランスをとりながら導入を進めることが可能になります。
PoCを検討する段階で、実現可能性の高いデモ開発を事前に確認しておくことも有効です。
エムニでは、各企業の業務課題や運用環境にあわせたカスタムAI開発のデモ提供を行っています。自社のユースケースに近い形でPoCの成功確度を高めたい方は、ぜひ以下のページもご参照ください。
補助金・支援制度の活用
デジタル化の取り組みを現実の施策へとつなげていくうえで、公的支援制度の活用は初期投資のハードルを下げる有効な手段となります。
「PoCから全社展開」へ進む段階では、技術的な検証に加えて、コストの妥当性にも目を向ける必要があります。
例えば「ものづくり補助金」では最大7,500万円、「IT導入補助金」では最大450万円まで、それぞれ補助率1/2を上限に支援が受けられます。
大型設備やロボットの導入には前者、クラウド型のMESや業務システムには後者が適しており、両制度は併用不可のため目的に応じた選定が必要です。
また、都道府県や市区町村が独自に提供するスマートファクトリー支援策などでは、補助率が3分の2に引き上げられるケースもあります。
こうした制度は公募時期が限られるため、事前に事業計画の骨子を整えておくことが、採択率向上のポイントになります。
支援制度は単なる費用補填ではなく、「今始める」ための後押しにもなり得ます。資金調達の選択肢を把握しておくことは、デジタル化のスピードとスケールを左右する重要な判断材料になります。
これからに向けた備え
技術の進化が著しい今、導入時には中長期的な視点と柔軟な設計が欠かせません。数年後に再投資やシステムの陳腐化に直面しないためにも、変化を前提にした対応力が求められます。
本章では、今後の製造業に関わる2つの重要テーマ――Industry 5.0とサステナビリティ、サイバーセキュリティと老朽システムのリスクについて解説します。
Industry 5.0とサステナビリティ
Industry 5.0は、効率と自動化を追求してきた従来の産業構造に対し、人間中心・持続可能性重視という新たな価値観を加えた次世代の産業ビジョンです。
欧州委員会がその概念を主導しており、環境負荷の低減や人と機械の協調を前提とした工場づくりが世界的に進みつつあります。
日本においても、カーボンフットプリントのリアルタイム計測やエネルギー使用量の可視化といった取り組みが広がり始めています。こうした環境指標を生産活動に組み込むことで、単なる法令対応にとどまらず、新たな競争力や取引条件の基盤となるケースも出てきています。
また、共同輸送や地域のカーボンリサイクル(CCU)など、サプライチェーン全体でのサステナビリティ連携も重視されつつあります。これは一企業だけでは完結しない課題であり、データ共有・連携の仕組みづくりが不可欠です。
製造業が持続的に成長していくためには、こうした社会的要請を自社のバリューチェーンに取り込むことが求められます。Industry 5.0は、その出発点を提示していると言えるでしょう。
サイバーセキュリティとレガシーシステム刷新コスト
デジタル化が進むほど、サイバーセキュリティは無視できない経営課題になります。特に製造業では、長年使い続けてきた老朽設備(レガシーシステム)をVPNでつなぐだけの暫定的な対応が多く見られますが、それでは現代の高度な攻撃には耐えられません。
近年では、ゼロトラストモデルを前提としたセキュリティ審査が標準化しつつあり、OT(制御系ネットワーク)領域の可視化と防御体制の再構築が求められています。実際、サイバー攻撃による平均損失額は5億円を超えるとも言われ、被害の深刻化により株価や企業価値が直接的に影響を受けるケースも出ています。
その一方で、老朽設備を丸ごと刷新するには多額の費用がかかり、すぐには着手できない企業も少なくありません。こうした現実を踏まえ、既存設備と新技術の共存を図りながら、段階的に安全性を高めていくハイブリッド型のアプローチが現実的な選択肢となっています。
サイバーセキュリティはもはや“保険”ではなく、事業継続の前提条件です。技術導入と並行して、情報資産の棚卸しやインシデント対応体制の整備を進めることは、今後の製造業にとって欠かせない取り組みです。
まとめ:デジタル化は、構想から実装へ
製造業におけるデジタル化は、もはや検討段階のテーマではありません。人材不足、設備老朽化、顧客ニーズの多様化といった構造的課題に対し、現実的な打ち手としての優先順位が一段と高まっています。
本記事で紹介したように、効果を上げている企業の多くは、「何を導入するか」ではなく「どこから始めるか」に明確な軸を持っています。KPIに基づいた段階的な導入、最小限からのPoC展開、将来を見据えた技術選定とリスク管理──いずれも重要なのは、目的に即した合理的な進め方を組織内で共有できているかという点です。
今後は、Industry 5.0やサステナビリティ、サイバーリスクといった外部要請への対応も避けては通れません。だからこそ、早い段階で構想を形に変え、現場での学びと修正を通じて前進できる体制を整えておく必要があります。
あとは最初の一歩を踏み出すだけです。成果を得ている企業は、すでに歩みはじめています。
エムニへの無料相談のご案内
エムニでは、製造業をはじめとする多様な業種に向けてAI導入の支援を行っており、企業様のニーズに合わせて無料相談を実施しています。
これまでに、住友電気工業株式会社、DENSO、東京ガス、太陽誘電、RESONAC、dynabook、エステー株式会社、大東建託株式会社など、さまざまな企業との取引実績があります。
AI導入の概要から具体的な導入事例、取引先の事例まで、疑問や不安をお持ちの方はぜひお気軽にご相談ください。
引用元:株式会社エムニ