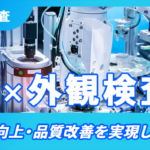
AIによる外観検査|目視検査との違いや成功事例も解説
2024-11-06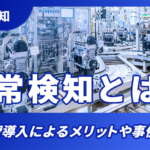
異常検知とは?機械学習導入によるメリットや事例を解説
2024-11-15外観検査の自動化|メリットから具体的な事例まで解説
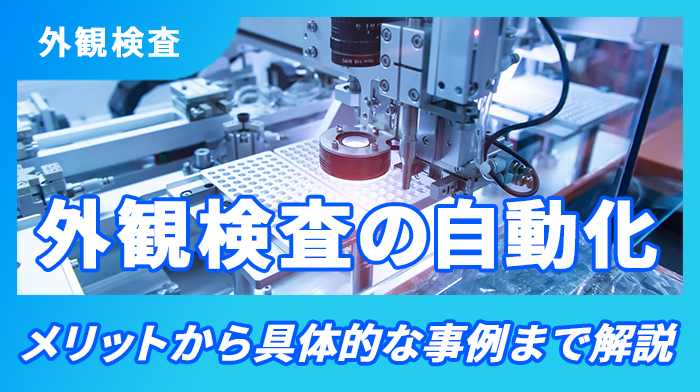
少子高齢化による人手不足が進む製造業において、外観検査の自動化は、もはや避けては通れない必須戦略です。自動化により人手不足の解消や検査精度の向上など多くの問題の解決が期待できます。
本記事では自動化を検討する上でその導入のメリットから注意点まで具体的な事例を交えて説明していきます。
外観検査の自動化とは
AIによる外観検査の自動化とは、製造業において、製品や部品の表面に現れる傷、汚れ、変形などの外観不良を、機械を用いて自動的に検出する技術です。自動化の手法は「ルールベース型」と「AI型」大きく二つに分けられます。
「ルールベース型」は予め人間が設定したルールに基づいて、画像の比較や特徴抽出を行うシステムです。初期コストが安く、単純なパターン認識には適していますが、新たな種類の不良や複雑なパターンに対応するには追加コストが発生し、また性能の向上にも限界があります。
「AI型」は、機械学習、特に深層学習を用いて、画像データを学習し不良品を検出します。「ルールベース型」と比較して必要なデータの数やシステム設計の手間が増すため初期導入コストは比較的高くなりますが、より柔軟に幅広いタスクに対応できます。
また近年は生成AIの登場によって、実際のデータから多様な擬似データを生成し、学習データの不足を補うことが可能になり、「AI型」の性能が飛躍的に向上しました。
▼AIによる外観検査について詳しく知りたい方はこちら
AIによる外観検査|目視検査との違いや成功事例も解説
どちらのシステムも、従来、熟練工の目視で行われていた検査作業を機械に置き換えることで、より客観的で高精度な検査を実現し、同時に生産性向上と人件費削減に貢献します。
外観検査を自動化するメリット
以下では主なメリットを5つ説明します。
精度の向上
人間による目視検査では、疲労や集中力の低下によってミスが発生する可能性があるだけでなく、主観的な判断が介入することによる基準のずれも発生しやすいため、製品品質にばらつきが生じやすいです。
一方、自動化された外観検査システムは、常にあらかじめ設定された客観的な基準に基づいて検査を行うため、検査者間のバラつきをなくし、常に安定した高品質な検査を実現できます。
さらに、AIを活用したシステムでは、新しい異常パターンを学習し続けるため、従来のルールベース型では対応できなかった微細な傷や異物を高い精度で検出することが可能です。
▼目視による外観検査の問題点について更に詳しく知りたい方はこちら
目視による外観検査の問題点と生成AIによる解決策を徹底解説
検査時間の短縮
機械はリアルタイム処理により人間よりも圧倒的に速く検査を行うことができるため、全数検査を効率的に実施できます。
従来はコストや時間的な制約から全数検査が困難な場合も多くありましたが、自動化により、全製品を高速かつ高精度に検査できるようになりました。これにより、生産ラインのサイクルタイムが大幅に短縮され、全体的な生産性が向上します。
コスト削減
AIによる外観検査の導入は、人件費の削減に大きく貢献します。従来、熟練した検査員が交代制で長時間行っていた検査作業を機械が担うことで、24時間365日の稼働が可能になり、人材育成コストや残業代の削減にもつながります。
さらに自動化は品質不良による損失の削減にも貢献します。人間の目では見つけにくい微細な傷や汚れも検出し、不良品を早期発見することでリコールコストの削減やブランドイメージの維持に繋がります。結果として、短期的な利益の増加だけでなく、長期的な利益の増加も十分に期待できるでしょう。
異常検知とデータドリブンな意思決定
外観検査の自動化には大量のデジタルデータが必要です。自動化に伴い、機器を導入することで大量のデジタルデータを短時間で高精度に収集し、分析に活用することができるようになります。
例えばAIを活用して、微細な欠陥やパターンを自動的に学習し、リアルタイムで高速なデータ分析を行うことで、生産ラインの異常を迅速に検知し、品質問題の発生を未然に防ぐことが可能になります。さらに、蓄積されたデータを活用することで、製品設計の最適化や新たな製品開発にも繋げることができます。
▼データ分析について更に詳しく知りたい方はこちら
「AI x データ分析」で経営戦略の精度が上がる
具体的な事例
外観検査の自動化は、自動車、食品、住宅など多くの業界で注目されています。以下では具体的な事例を紹介していきます。
トヨタ自動車
トヨタ自動車は、WiseImagingのAI画像解析技術を導入することで、磁気探傷検査の自動化に成功しました。従来、熟練した検査員が磁粉などを用いて目視で行っていた検査にAIの画像解析を導入したことで、見逃し率 0%、過検出率8%と優秀な数値を達成しました。
またフロントハブの検査工程に関わる従業員は、これまで二交代勤務で計4名でしたが、磁気探傷検査を自動化することができ、2名の省人化を実現しました。
日産自動車
日産自動車は、栃木工場の「日産アリア」生産ラインに、塗装品質の自動検査システムを導入しました。このシステムは、従来、熟練の検査員が身体的負担を負いながら行っていた0.3mm程度の微細なゴミや塗装ムラなどの検出を、ロボットが自動で行うものです。システム導入により、塗装品質の安定化、生産性の向上、そして従業員の働き方改革という、多くの効果が期待できます。
ニチレイフーズ
ニチレイフーズは、AIによる選別検査装置を導入しています。不良品との基準範囲境界に近い商品は判断が難しく、「念のため廃棄」が多発してしまうという問題がありました。そこでえびに特殊な光を当てて殻と身の反応の違いにより殻を自動で取り除く装置を20年以上前から開発し、実用化しています。
また近年は長年培ってきた選別検査の技術にAIを組み合わせ、チキン原料を特殊なカメラで撮影し、画像の血合いや羽の部分を独自のアルゴリズムで数値情報化して判定するシステムを開発しました。
これらのシステムは工場に導入され、フードロス削減と人手不足解消に大いに貢献しています。
キユーピー
キユーピーは、惣菜の原料となるカット野菜の検査に、AIを活用した自社開発の原料検査装置を導入しました。具体的にはニンジンの検査工程に、大量の良品データを学習させた検査AIを導入し夾雑物などの混入を検知しています。「シンプル&コンパクト」な操作性を持つ検査装置によって作業者の身体的負担を削減し、業務を効率化しました。
積水ハウス
積水ハウスは、カメラと LED 照明を組み合わせて VisionPro Deep Learning を導入し、製造プロセス全体の外観欠陥検査を自動化しました。VisionPro Deep Learningはディープラーニングをベースとしたツールで少量の画像データから高精度の欠陥検出を可能とします。
すべての部品を自動的に検査することで、予備生産量の 0.4% を占めていた不動在庫を 40% 減少させ、ベルバーンセラミックタイルの供給を安定させることに成功しました。
外観検査自動化を実現するにあたっての障壁
外観検査の自動化には、いくつかの障壁があります。これらをあらかじめ理解することで想定外のトラブルが少なくなりスムーズにプロジェクトを進めることが可能です。
コスト
自動化システムの導入には高額な初期投資が必要です。機器の購入費用だけでなく、既存の生産ラインの見直しや、検査基準を学習させるためのデータ作成など、さまざまなコストが発生するため、導入だけで数百万円以上のコストがかかることも多々あります。
また自動化のシステムは、特定の製品や部品に合わせてプログラムを調整する必要があります。汎用性が低いため、異なる形状や材質の製品に対しては再設定が求められます。
技術的な難しさ
自動化には、製品ごとに異なる仕様に合わせた検査機器のカスタマイズが必要です。多くの企業が、独創的な製品の開発やオリジナル装置の開発を行っており、導入の大きな障壁となっています。
特に、多様な製品を扱う工場では、自動化が難しいとされています。多品種少量生産の場合、各製品に対して自動化機器の詳細なカスタマイズや設定が必要となり、導入の難易度が高いです。
人材不足
自動化を進めるためには、機器の操作やプログラミングを行う「ティーチングマン」の育成が不可欠です。しかし、熟練した人材の確保が難しく、育成には数年かかることもあります。このため、希望する時期に人材を確保できない場合や、高いコストが発生することがあります。
外注することも選択肢の一つですが、その場合、継続的に費用がかかることや社内の人間にノウハウがたまらないことなど新たな問題が発生するのでよく検討して決定することが重要です。
外観検査自動化プロジェクトの進め方
外観検査自動化プロジェクトを成功させるための具体的な手順を説明します。
ステップ1:要件定義
外観検査の自動化を成功させるには、単に「自動化したい」という漠然とした目標ではなく、数字を掲げることが非常に重要です。
「不良品率を現在の10%から2%に下げる」や「検査時間を30%短縮する」といった具体的な数値目標を設定することで、システムに求められる機能や性能、制約条件などを明確に定め、円滑に導入することが可能になります。
コストや実現可能性などを意識しながら、以下の表を参考に可能な限り綿密な計画を立てましょう。
項目 | 例 |
目的 | スマートフォン組み立てラインにおけるカメラモジュールの外観検査工程を自動化 |
対象製品 | スマートフォン用カメラモジュール |
検査項目 | ・レンズ面の傷、汚れ・異物混入 |
検査環境 | 照明条件:均一な拡散照明温度:20℃~25℃湿度:50%~60% |
システム機能 | 画像取得:高解像度カメラによる画像取得画像処理:画像の前処理、特徴抽出、欠陥検出判定:良品/不良品の判定 |
性能 | 検査速度:1個/秒検出精度:傷の大きさ0.1mm以上の検出誤検出率:1%以下 |
インターフェース(他システムとの連携) | MESシステムとの連携:検査結果の連携、生産管理システムとの連携 |
スケジュール | 要件定義:9月(期間:2週間) システム設計:10月(期間:4週間) プロトタイプ作成:11月(期間:4週間) 精度改善:12月(期間:4週間) 本番稼働:1月〜 |
予算 | 【初期費用】 開発費用:500万円 【ランニング費用】 サーバー費用:5万円/月 生成AI API利用料:一人当たり150円/月 |
ステップ2:システムの構築
要件定義で明確化された内容に基づき、外観検査システムを実際に構築していきます。まず、システムの性能要件、コスト、既存システムとの連携性といった重要な要素を念頭に置き、ハードウェアとソフトウェアの選定を行います。
ハードウェア選定では、検査対象物の特性や検査項目に最適なカメラ、照明、コンピュータなどを決定します。高解像度で微細な欠陥を検出できるカメラや、均一な照明で影を少なくする照明など、検査の精度を左右する要素を慎重に検討します。また、画像処理の負荷に耐えうる十分な処理能力を持つコンピュータを選択することも重要です。
ソフトウェア選定では、要件定義の基準を満たす精度の画像処理アルゴリズムを搭載し、直感的な操作性を備えたソフトウェアを選びます。さらに、既存のシステムとの連携をスムーズに行えることも重要なポイントです。
そして選定したハードウェアとソフトウェアを基に、システム設計を行います。カメラの設置位置、照明の角度、画像処理の処理フローなどを詳細に設計することで、より効率的で高精度の検査システムを実現できます。
ステップ3:テスト
システム構築が完了したら、実際にシステムが正しく動作し、要件を満たしているかを確認するためのテストを実施します。テストは、システムの品質を保証し、不具合を早期に発見するために不可欠な工程です。
「データ欠損値の処理が正しく行われているか」「特徴量のスケーリングが適切か」といった細かい内容から、「大量のリクエストが同時に発生した場合のパフォーマンス」「ネットワーク遅延が発生した際の動作」「異常な入力データへの耐性」などといった総合的な内容まで、様々な観点からの検証を行います。
再現性や網羅性に注意しながら要件定義で定めた基準を満たせるかどうか念入りに検証しましょう。
ステップ4:本導入と運用
テストの結果が良好であれば、いよいよシステムを実際の生産ラインに導入し、本格的な運用を開始します。システムの本導入は、これまでの開発・テスト段階の成果を実際の現場で実証する重要なステップです。
まず既存システムとの連携や、従業員への教育なども考慮しながらシステムの導入時期、導入範囲、移行手順などを詳細に計画します。計画が策定できたらデータの移行、設定の変更、ネットワーク接続などを慎重に行いながらシステムを本番環境に移しましょう。
またシステムを安定稼働させるために、専用の運用チームを編成したり、既存のチームに担当を割り当てたりすることも必要です。定期的なパトロール、障害対応、バックアップなど、運用に必要な業務を明確化し、責任者を定めます。
導入初期は特に注意深くシステムの挙動を観察し、問題が発生した場合には迅速に対応する体制をあらかじめ準備しておきましょう。PDCAサイクルを回すことを意識し継続的な改善を行うことが重要です。
ステップ5:データ収集と分析
外観検査システムは、単に製品の良否を判定するだけでなく、収集されたデータを活用することで、より高度な品質管理を実現するための重要な情報源となります。自動化を達成して終わりではせっかく収集可能になったデータがもったいないため、積極的に活用することが重要です。
例えば、不良品の画像データを詳細に分析することで、不良の種類や発生箇所を特定できたり、製品品質の長期的な変化が捉えられたりします。新しく得られたデータをAIに学習させることで、さらにシステムの性能を向上させることも可能です。
ただし、AIのパフォーマンスはデータの質に大きく左右されるため、収集したデータが正確かつ信頼できるものであり、分析対象となる全体を代表するような偏りの少ないものであることは慎重に確認した方がいいでしょう。
外観検査自動化を成功させるために
外観検査の自動化は、自社のニーズに合った外観検査自動化システムを構築することが成功への鍵となります。以下では主要なポイントを3つ挙げて説明します。
データ取得環境の慎重な整備
外観検査を自動化する際にはカメラ、照明、画像処理装置などのハードウェアが必要です。これらの機器はそれぞれ多様な種類があり、また検査を実際に行う環境も導入先によってバラバラであるため、製品の特性に応じて慎重に選ぶ必要があります。
カメラ選定では、検査対象の最小欠陥サイズに基づく解像度、製品搬送速度に合わせたフレームレート、視野範囲とのバランスを考慮したセンサーサイズを検討します。色味検査の要否によるカラー・モノクロの選択も必要です。
照明システムは、検査目的に応じて照明の当て方(同軸落射照明、リング照明、バックライト、ドーム照明)から最適なものを選択します。光源はLED、蛍光灯、キセノン、レーザーなどがあり、それぞれ特性が異なります。波長も可視光、赤外線、紫外線、偏光から目的に応じて選定します。
画像処理装置では、アルゴリズム実行やディープラーニング推論に必要な処理性能、画像データ保存用のメモリとストレージを確保します。設置環境での振動、温度変化、粉塵、電磁ノイズへの対策も検討が必要です。
これらの機器を組み合わせた後は、基本性能の確認、環境耐性テスト、異常時の動作確認を行い、実運用での検査精度、操作性、メンテナンス性を総合的に評価します。全ての要素の整合性を確認することで、高精度で安定したシステムを実現可能です。
ソフトウェアの比較検討
ソフトウェア選定においては、検査対象物と検査機器に合わせてソフトウェアの機能、導入企業の環境、ベンダーのサポート体制、そしてコストといった多岐にわたる要素を総合的に検討しましょう。
また、自社製品の独自性が強く、既存のソフトウェアで対応が難しい場合には、カスタム開発が必要となることがあります。カスタム開発を外部の企業に依頼する場合、丁寧なデモ開発を行うことが非常に重要です。この過程で、要件定義と実際の仕様のずれを細かく修正していくことで、最終的に本導入および運用の段階における重大なミスの発生リスクを最小限に抑えることができます。
人材の育成
外観検査の自動化は、システムの導入だけでなく、人材育成も非常に重要な要素です。システムを最大限に活用し、安定稼働させるためには、専門知識を持った人材の育成が不可欠です。
外部研修やOJT、社内勉強会などを通じて、システムの運用・管理、トラブルシューティング、さらには改善提案を行える人材を育成することで、自動化システムの安定稼働を確保することができます。
外観検査を自動化するに当たっての注意点
外観検査の自動化にはいくつかの注意点があります。これらのポイントを意識することでさらなる成果が見込めます。
データの量と質にこだわる
外観検査の精度を根本から支えるのはデータです。どんなに性能のいいソフトウェアでもデータが揃っていなければ中途半端な精度の検査しかできません。
データの量、種類を十分に確保しアノテーション(データのラベル付け)の精度にこだわり、良品データと不良品データのバランスを適切に設定することが外観検査の精度向上に直結します。
また画像データに影や反射が発生しないように均一な照明環境を構築することもとても重要です。光源の種類や角度にこだわって質のよいデータを作成しましょう。
閾値設定を最適化する
自動検査では、合否判定を行うための閾値を設定します。この設定を最適化することで誤検出や見逃しを減らし、より高精度な検査が可能です。
安定した判定を得るためには、繰り返しテストと調整を行い最適化することが必要不可欠です。統計的手法を活用したり、定期的に専門家の人の目による調整を加えながら最適な境界値にこだわりましょう。
完全自動化が最適解とは限らない
外観検査へのAI導入において、全工程の完全自動化が必ずしも最適解とは限りません。
AIは高速で正確な処理、定量的な判定、膨大なデータの学習と分析において優れた性能を発揮しますが、人は新たな不良パターンの発見や、複数の要因を組み合わせた総合判断、想定外の状況への対応に優れています。製品の微妙な質感の変化や、これまでに見たことのない異常の検出、複雑な背景を考慮した判断は、人間の方が向いていると言えるでしょう。
実践的なアプローチとしては、AIと人間それぞれの強みを活かした検査体制の構築が効果的です。AIによる一次スクリーニングで明確な良品・不良品を選別し、判定が難しいグレーゾーンの製品は人間が確認するというオペレーションも考慮するといいでしょう。また、AIの判定結果を人間が定期的に検証し、判定基準の微調整や新しい不良パターンの学習データとして活用することで、システム全体の精度を継続的に向上させることができます。
製品の重要度や不良の影響度に応じて、検査方法を使い分けることも効果的です。重要部位の検査や致命的な不良の検出には、AIと人間の両方による確認を行い、比較的影響の少ない項目はAIによる自動検査のみとするなど、メリハリのある検査体制を構築することで、より効果的な品質保証を実現できます。
まとめ:熟練工の目と手を継承する、自動化が導く製造業の未来
AI技術の急速な発展により、外観検査の自動化は新たなステージを迎えています。
特に深層学習による画像認識技術は、熟練工が長年の経験から培ってきた「勘」や「経験」を学習し、従来では見つけられなかった微細な不良を検出できるようになりました。最新の技術の動向に目を向けて、導入できそうなものは積極的に導入を試みることが重要です。
また、製品の特性によっては既存のソフトウェアだけでは十分な対応が難しい場合があります。例えば、独自の製造工程や特殊な検査基準、複雑な形状の製品など、標準的なソリューションでは解決が困難なケースも少なくありません。
このような課題に直面されている企業様に、エムニではカスタマイズ可能なソリューションをご提案しております。まずは御社の具体的な課題やニーズをお伺いし、実現可能な解決策を一緒に検討させていただきます。
エムニへの無料相談のご案内
エムニでは、製造業をはじめとする多様な業種に向けてAI導入の支援を行っており、企業様のニーズに合わせて無料相談を実施しています。
これまでに、住友電気工業株式会社、DENSO、東京ガス、太陽誘電、RESONAC、dynabook、エステー株式会社、大東建託株式会社など、さまざまな企業との取引実績があります。
AI導入の概要から具体的な導入事例、取引先の事例まで、疑問や不安をお持ちの方はぜひお気軽にご相談ください。
引用元:株式会社エムニ