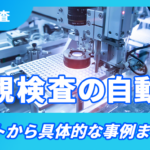
外観検査の自動化|メリットから具体的な事例まで解説
2024-11-08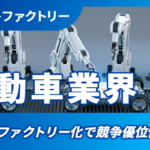
自動車業界のスマートファクトリー化|メリットや事例
2024-11-17異常検知とは?機械学習導入によるメリットや事例を解説
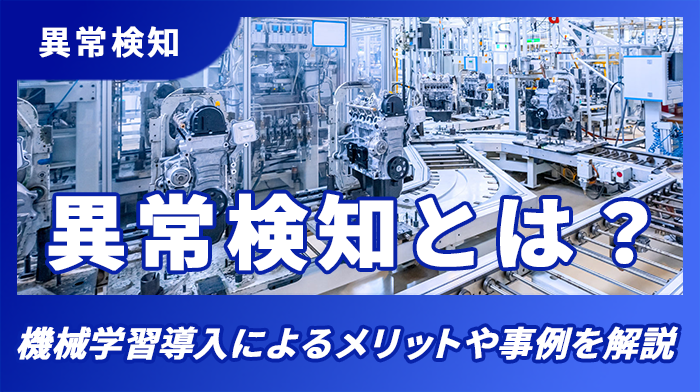
大量のデータの中から正常なパターンとは異なるものを特定する技術である異常検知。異常検知による製造行程と品質の安定性は企業の競争力そのものと言っても過言ではありません。
異常検知に機械学習を導入することで、製造機器のリアルタイム分析による故障の早期発見、品質検査結果の効率的な解析による不良品の早期排除を実現できます。貴社の異常検知に機械学習を導入し、工場のスマートファクトリー化を実現しましょう。
本記事では、異常検知に機械学習を導入するメリットから、実際の成功事例、さらに導入に際してのロードマップまで詳しく解説していきます。
異常検知に機械学習を導入するメリット
異常検知に機械学習を導入することで得られる多くのメリット。機械学習の導入がもたらす業務改善について詳しく見ていきましょう。
異常検知全体に共通するメリット
従来のルールベースの異常検知システムに比べて、実際のデータに基づいて判断する機械学習では、誤検知や未検知を大幅に削減。また、機械学習モデルは導入後も新しいデータに基づいて継続的に学習・改善できるため、工場の規模や製品ラインの変化への柔軟な対応が可能に。さらに、自動化された異常検知によって人手による作業が減少。長期的に見ると人件費や検査費用の面で大きなメリットがあります。
加えて、熟練工のノウハウをデータとしてAIに学習させることで、熟練工に属人化していた異常や欠陥のパターンの知識をデジタル化できます。これにより、熟練工だけが持っていた暗黙知を誰でも利用することが可能となり、技能伝承がより簡単に行えるようになるでしょう。
ここからは、予知保全および製品検査の観点から詳しくメリットを見ていきましょう。
予知保全におけるメリット
機械学習モデルの導入により製造機器のリアルタイムモニタリングが実現。異常が検出された場合の即時対応が可能になります。また、機械学習モデルでは過去のデータをもとに設備の異常兆候を早期に検出できるため、故障前の保守対応も実現可能です。
さらに、不要な定期メンテナンスを廃止し最適なタイミングでメンテナンスを実施することで、ダウンタイムが減少、生産ラインの停止時間を最小限に抑えることができます。
製品検査におけるメリット
データを用いる機械学習モデルでは、高精度な自動検知により、人間の目視検査よりも誤検出や未検出が減少。また、従来の統計的手法では分析が難しかった、画像データ、音声データ、テキストデータなど複数のデータを組み合わせることで、より精度の高い異常検知を実現できます。
さらに、多様な異常パターンを機械学習モデルが自動的に学習し、新たな欠陥の検出にも対応可能です。加えて、検査プロセスが自動化されることで、従来の手動検査よりも迅速な不良品の検出が行えるようになります。
異常検知への機械学習導入の成功事例
異常検知システムへ機械学習の導入に成功した事例をご紹介します。競争に遅れを取らないために、まずは他者の事例を知ることから始めましょう。
キユーピー株式会社
キユーピーでは、食品工場の製造ラインでの不良品検知に機械学習を導入しています。ディープラーニングを用いた画像解析技術を活用し、製品の良品・不良品を瞬時に判別するアルゴリズムを開発。これにより、人間の目視では難しい微細な異常を高精度で検出することが可能になり、品質管理の効率化を実現しています。
参考記事:ブレインパッド、キユーピーの食品工場における不良品の検知をディープラーニングによる画像解析で支援
ヤンマー株式会社
ヤンマー中央研究所では、内燃機関の予知保全のために機械学習を導入。内燃機関の状態をリアルタイムで監視する異常検知システムを構築しました。これにより、設備の健康状態をリアルタイムで可視化し、故障の早期予測が可能になっています。
参考記事:ヤンマー株式会社 中央研究所:異常検知プラットフォーム導入事例
ナブテスコ株式会社
ナブテスコでは、風力発電機のヨー旋回部の状態監視に機械学習を活用。異常検知システムの導入により、設備の負荷状態をリアルタイムで可視化し、保守作業の効率化を図っています。また、過去に発生した異常状態の詳細も履歴として閲覧可能になりました。
参考記事:ナブデスコ株式会社:異常予兆検知プラットフォーム導入事例
JFEケミカル株式会社
蒸留塔の熱交換器が閉塞するトラブルに対して、機械学習を利用した異常予兆検知のシステムを導入。これまで事後保全的な対応しかとれていなかったが、事前に設備の詰まり具合を把握できることで、設備保全のタイミングの最適化が可能となりました。
株式会社オプテージ
従来の閾値ベースでの監視では検知が困難だったサイレント障害に対して、機械学習を用いた異常検知を導入することで、検知漏れなし、かつ誤検知を99%削減することに成功。ネットワークの急激なトラフィック減少を10分以内に検知可能になりました。これにより、システム運用効率と信頼性が大幅に向上しました。
参考記事:株式会社オプテージ:サイレント障害の監視基盤導入事例
異常検知への機械学習導入における課題
機械学習の導入のためには、多くの克服すべき課題が存在します。まずは課題を正確に把握し、どのように取り組むのかを知ることから始めましょう。
大量かつ高品質なデータの収集
機械学習の性能を左右するのは、データの質と量です。そして、製造現場でのデータ収集では、センサーのノイズを除去する・異常データの収集を工夫する・正常データと異常データの量のバランスをとる、といった課題が存在します。
センサーの測定値については、工場内の振動や電気的な干渉により、データが乱れてノイズが発生してしまう場合があります。これは、データの平均を取って滑らかにしたり(移動平均フィルタ)、ノイズを予測して除去したり(カルマンフィルタ)することで対処できます。この様な処理に加えて、定期的なセンサーの調整も基本的かつ重要な要素です。
次に異常データの収集について。実際の製造現場では故障は稀なので、学習に必要な異常データが集まりにくいのが悩みどころです。この場合、AIが本物そっくりの異常データを作り出したり(GANs・VAE)、既存の異常データに少し変化を加えて数を増やしたり(Data Augmentation)する方法で対応します。
さらに、正常データと異常データの量が極端に違う場合も。異常が少なすぎると、AIは「すべて正常」と判断しがちになってしまいます。そこで、異常データを人工的に増やしたり(オーバーサンプリング)、正常データを減らしたり(アンダーサンプリング)して、バランスを取ります。
加えて、センサーが一時的に故障すると欠測が発生します。この場合、前後のデータから推測して補完したり(線形補間)、AIに予測させたり(RNN)して対処します。
適切な機械学習モデルの構築
機械学習には多様なモデルが存在するため、どのようなモデルを選択し、どのようにチューニングするかが重要です。
統計的手法をベースにした単純なモデルでは、平均値や標準偏差から大きく外れたデータを異常と判定します。解釈が容易で、計算コストも低いため、製造ラインの基本的な品質管理でよく活用されています。
サポートベクターマシン(SVM)やランダムフォレストなどの従来型の機械学習モデルは、複数のデータの特徴を組み合わせて異常を検出できます。判断の過程を人間が理解しやすく、製造現場での説明性が求められる場合に適しています。
深層学習(ディープラーニング)は、画像や音声など、複雑なデータパターンの認識に優れた手法です。ただし、なぜその判断に至ったのかが不明確になりやすい「ブラックボックス問題」が存在します。
この問題を解決するため、最近では「説明可能なAI(XAI)」の開発が進んでいます。LIME(Local Interpretable Model-agnostic Explanations)やSHAP(SHapley Additive exPlanations)といった技術により、AIの判断根拠を人間にもわかりやすく示すことができるでしょう。
適切なモデルは現場の要件によって変わります。重要なのは、説明性、精度、計算コスト、運用の容易さなど、様々な要素のバランスを考慮することです。
リアルタイム対応の確保
製造現場の異常検知をリアルタイムで実現するには、高速なデータ処理基盤の整備が必要不可欠です。
効率的なリアルタイムデータ処理では、センサーから送られる大量のデータを素早く分析し、異常を即座に検出する必要があります。このため、高性能な計算資源とエッジコンピューティングの活用が重要です。製造現場に近い場所にデータ処理装置を設置することで、クラウドへの転送時間を削減し、異常の即時検出が可能になります。
異常を検知した際の自動対応も重要な要素です。システムが異常を検出すると、直ちにアラートを発信し、必要に応じて設備の緊急停止などの安全措置を自動実行します。これにより、異常発生から対応までの時間を最小限に抑え、被害の拡大を防止できます。
さらに、システムには高い拡張性も求められます。生産ラインの増設や新規センサーの追加に柔軟に対応できるよう、クラウドベースのソリューションや分散処理技術を活用します。これにより、データ量の増加にも対応可能な、スケーラブルなシステム構築が実現可能です。
AI人材の育成
AI人材の育成は、異常検知システムの導入と運用において重要な課題であり、AI人材に求められる専門知識は多岐にわたります。機械学習やディープラーニングの理論的理解はもちろん、統計学やプログラミングのスキル、データ分析の実践力が不可欠です。さらに、AIが出力した結果の解釈や、問題発生時の原因究明能力も重要となります。
急速に進化するAI技術に対応するため、継続的な学習も必要です。オンライン講座やワークショップへの参加を通じて、最新技術のキャッチアップを行いつつ、製造現場特有の課題を理解し、現場エンジニアとの円滑なコミュニケーションを図る能力も求められます。
人材育成のアプローチとしては、段階的な方法が効果的です。導入初期は外部専門家の支援を受けつつ、OJT(On the Job Training)を通じて社内人材の育成を進めまるといいでしょう。実際のプロジェクトに参加させることで、実践的なスキルとノウハウを蓄積させていきます。
異常検知への機械学習導入ロードマップ
機械学習の導入は一朝一夕には進みません。しっかりとした計画を立案し、着実に導入を進めることが重要です。以下に示すロードマップを参考に、計画的な機械学習の導入を目指しましょう。
1. 現状分析と目標設定
まず、現状の異常検知の分析を行います。具体的には、現状のシステムが抱える課題、未検知や誤検知の有無などを確認。また、生じている損失(コスト増、品質低下、生産ダウンタイム)を計算します。
さらに、センサーの配置状況やデータの収集体制など、既存の異常検知システム体制を把握することも重要です。これら現状分析を通じて、機器の故障予測や製品の欠陥検知など「何を異常として検知したいのか」を明確化します。
次に、目標設定を行います。検知精度、誤検知率、異常対応時間など、定量的な目標設定を目指します。ROI(投資利益率)の試算のために、コスト削減や効率向上の見積もりを行いましょう。
同時に、システムの運用負荷低減や現場スタッフにとっての使いやすさなど、定性的な目標も必要です。最後に、短期・中期・長期の導入スケジュールを設定し、段階的な評価と改善を組み込んだ実行計画を立てることが成功に繋がります。
2. データ収集と事前処理
異常検知システムの構築に向けたデータ収集と事前処理は、成功の鍵を握る重要なプロセスです。
データ収集では、まず目的に応じた適切なデータソースを特定します。温度、振動、圧力などのセンサーデータ、設備の稼働ログ、検査記録、画像データなど、異常検知に必要な情報を明確化しましょう。データの量と質を確保するため、長期間にわたる正常時のデータと、可能な限り多くの異常事例のデータを収集する必要があります。
収集したデータは、機械学習モデルで活用できるよう適切な前処理が必要です。センサーノイズの除去や欠損値の補完、外れ値の処理といったデータクリーニングを実施します。また、異なるスケールのデータを統一するため、標準化や正規化も重要なステップとなります。
時系列データからは、傾向や周期性といった特徴を抽出します。これにより、異常の予兆を捉えやすくなります。画像データの場合は、解像度の調整やノイズ除去、特徴量の抽出などの処理が必要です。
最後に、データをトレーニング用、検証用、テスト用に分割します。この分割により、モデルの性能を客観的に評価し、過学習を防ぐことができます。異常データが少ない場合は、正常データを中心とした学習アプローチを検討します。
3. 機械学習手法の選定と運用システムの開発
機械学習手法の選定では、データの特性と目的に応じた適切な手法を選択します。構造化データには統計的手法やサポートベクターマシン、画像データには畳み込みニューラルネットワーク、時系列データにはLSTMなど、それぞれのデータ特性に最適なアルゴリズムを採用します。
精度と解釈性のバランスも重要です。製造現場では、モデルの判断根拠を説明できることが重要となるため、決定木やランダムフォレストなど、解釈が容易なモデルが好まれます。
また、運用システムの開発では、MLOpsの導入が不可欠です。モデルの継続的な学習とデプロイ、パフォーマンス監視、必要に応じた再学習を自動化することで、安定した運用を実現します。
加えて、セキュリティとコンプライアンスにも十分な配慮が必要です。データの暗号化、アクセス制御、監査ログの記録など、包括的なセキュリティ対策を実施しましょう。また、データ保護に関する法規制への準拠も確実に行う必要があります。
4. システムの試験と現場導入
異常検知システムの試験と現場導入は、慎重なステップを踏んで進める必要があります。
試験フェーズでは、まずデータ処理やモデル推論など各機能の単体テストを行います。続いて、システム全体の統合テストで、データフローやモデルの判定結果が期待通りかを検証。
セキュリティテストでは、データ保護や不正アクセス対策の有効性を確認し、最後に実際のユーザーによる受け入れテストで業務要件の充足を見極めます。
現場導入は段階的なアプローチを取ります。最初に小規模な環境でパイロット導入を実施し、実運用での課題を洗い出します。この際、現場作業員からの詳細なフィードバックを収集し、操作性や機能の改善に活用。異常検知の精度や応答速度、誤検知率などの定量的な評価も欠かせません。
パイロット導入での知見を基に必要な改善を加え、全面展開へと移行。この段階では、ユーザートレーニングが極めて重要となります。システムの仕組みや操作方法、異常検知時の対応手順について、十分な教育を実施しましょう。
導入後も継続的なサポートとメンテナンスが必要です。システムの監視、トラブル対応、定期的な性能評価を行い、必要に応じて更新や調整を実施。これにより、長期的な運用の安定性を確保することが可能です。
5. 継続的な評価と改善
異常検知の定期的なパフォーマンス評価では、誤検知率、応答時間などの定量指標を継続的に監視し、目標値との乖離を分析して必要な改善策を検討します。運用コストの分析も欠かせず、システムの維持管理に要する実際のコストを把握し、費用対効果を評価することが重要です。
加えて、新規データの収集と蓄積を継続し、モデルの定期的な再学習を実施してデータ品質の維持向上にも取り組みましょう。これにより、製造環境の変化や新たな異常パターンへの対応力を強化します。現場作業員からのフィードバックも積極的に収集し、システムの改善に活用していきます。
技術面での最適化も継続的に行います。異常検知アルゴリズムの性能評価を定期的に実施し、より高精度な手法が登場した場合は導入を検討しょう。システムのスケーラビリティやセキュリティ対策も随時見直し、必要に応じて強化を図ることも大切です。
異常検知への機械学習導入における4つの注意点
機械学習導入を妨げる様々な注意点。以下に示す4つのポイントに十分に注意し、機械学習の導入を成功に導きましょう。
誤検出と未検出の可能性
異常検知システムが持つ誤検出(正常を異常と判断)や未検出(異常を見逃す)のリスクには注意が必要です。
誤検出が多いと、無駄な対応が増え、作業効率が低下し、現場の信頼も損なわれる可能性があります。一方、未検出は設備故障や製品不良の見逃しに繋がり、コストや品質に直接的なダメージを与えます。
これを最小限にするためは、データのノイズ除去や欠損値補完による機械学習モデルの精度向上が不可欠です。さらに、リスク許容度を設定し、業務影響を見極めたうえで、適切な検知基準を設けることが求められます。また、人によるモニタリングでAIの判断を検証し、システム改善に役立てる体制を整えましょう。
情報セキュリティのリスク
機械学習モデルには大量のデータが必要であり、データ漏洩や不正アクセスのリスクが高まります。そのため、クラウドを含めたシステム全体でセキュリティ対策を講じる必要があります。
ネットワークのファイアウォールやデータの暗号化など、外部からのサイバー攻撃に対する防御策(システムセキュリティ)に加えて、アクセス権限の管理や社員へのセキュリティ教育など、社内での安全な運用を確保するための対策(運用セキュリティ)を組み合わせることで、セキュリティレベルを向上させましょう。また、セキュリティやコストの条件によっては、オンプレ環境でのシステム開発も視野に入れましょう。
導入・運用コストの大きさ
異常検知システムの開発には、データ収集や機械学習モデルおよびインフラの構築にかかる様々なコストがかかります。また、初期費用として、ハードウェア購入や人材確保にかかる費用も考慮に入れる必要があります。また、継続的なデータ収集とモデル学習、システムの維持管理など、導入後も継続してコストが必要となることにも注意が必要です。
実際の導入時には、現場での課題優先度に基づく段階的な導入計画を策定し、初期コスト低減を図りましょう。また、導入計画を立てる際には、将来的な投資回収やスケールアップを見込んだ戦略立案を目指します。
さらなるコスト削減には、シンプルなシステムを構築することによる運用コストの削減なども有効です。
予測過程の不透明さ
高度な予測能力の一方で、機械学習モデルの予測過程はブラックボックスになりがちです。なぜそのデータが異常と判断されたのかを説明できなければ、現場担当者の不信感につながり、システムの導入に支障をきたす恐れも。これを防ぐには、予測の根拠を人間が理解できるように説明する能力を持つ、説明可能なAIの導入が有効です。
ユーザーのトレーニングも重要です。機械学習モデルや異常検出システムの理解度を向上させ、AIが導いた予測の解釈や問題発生時の原因特定など、運用スキルの習得が求められます。また、技術の進歩やビジネス環境の変化に対応するため、継続的な学習に取り組みましょう。
興味がある方向け:異常検知に用いられる機械学習手法
異常検知に用いられる機械学習手法についても詳しく解説いたします。こちらの内容は特にエンジニアが知っておくべき内容なので、完璧に理解しておく必要はありません。
教師あり学習
教師あり学習は、データに明確な「正解」を付与してAIを学習させる手法です。製造ラインで言えば、「この振動パターンは正常」「この画像は不良品」といった具体的な答えをセットにして学習を進めていきます。
正解データがあることで、AIは何が正しく何が間違っているかを明確に理解できるため、高い精度が期待できるのが特徴。例えば製品検査では、熟練検査員が判定した結果をもとに学習することで、人間に近い判断能力を身につけることが可能になります。
一方で、大量の正解データを用意する必要があるという課題も存在しています。熟練者による判定作業には多大な時間とコストがかかり、特に異常データについては実例の収集自体が困難なケースも多いのです。
そのため実務では、最初は少量の確実な正解データで基本的な学習を行い、運用しながら徐々にデータを増やしていくアプローチが効果的とされています。
教師なし学習
教師なし学習は、正解ラベルを必要としない機械学習の手法です。大量の生データからAI自身が特徴やパターンを見出していきます。
製造現場では、通常の操業データから機械の正常な動作パターンを自動的に学習。そこから逸脱する異常な挙動を検知することが可能になります。ラベル付けの手間が不要なため、膨大な運転データを効率的に活用できるのが利点です。
しかし、AIが検出したパターンが本当に意味のあるものかどうかの判断は難しく、誤検知のリスクも存在。また、なぜその判断に至ったのか根拠を説明することが容易ではないという課題も抱えています。
そのため実務では、教師なし学習で異常の可能性がある事象を幅広く検出し、その後人間の専門家が詳細に分析するという組み合わせ型のアプローチが効果的とされているのです。
半教師あり学習
半教師あり学習は、教師あり学習と教師なし学習の利点を組み合わせた手法です。少量の正解ラベル付きデータと、大量のラベルなしデータを併用することで、効率的な学習を実現します。
製造現場では、熟練検査員が判定した少数の確実なデータと、日常的に収集される大量の未判定データを組み合わせて活用することで、限られた正解データでも高精度な異常検知モデルの構築が可能になります。
ラベルなしデータを活用することで、データの全体的な分布や構造を把握できるのが特徴的です。一方、品質の低いラベルなしデータが混入すると、モデルの性能が大きく低下する可能性もあるため、データの品質管理が重要な課題と言えます。
実運用では、最初に少量の確実なラベル付きデータで基本的な学習を行い、その後ラベルなしデータを段階的に追加していくアプローチが推奨されています。このように慎重にデータを選別しながら学習を進めることで、効率的かつ信頼性の高いモデルを構築することが可能です。
まとめ:機械学習が実現する異常検知の革新
機械学習の導入によって実際のデータに基づいた異常検知が可能に。システムの精度や効率を大幅に向上することができます。加えて、機械学習の導入は、熟練工に属人化したノウハウのデータ化・標準化を実現し、技能伝承にも大きく貢献します。
このように多くのメリットを持つ一方で、機械学習の導入に求められる入念な準備と対策。膨大なデータの収集とクリーニング、適切な機械学習手法の選定とシステム構築、導入後の継続的な評価と改善など、実現までに取り組むべき課題は山積みです。
そのため、まずは社外の専門家に相談し徐々に内製化を進めることで、リスクを抑えつつ効率よく機械学習を導入した異常検知を実現するとよいでしょう。
弊社では製造業に特化したAI導入、および企業様と伴走しながらの継続的な支援を行っております。技能伝承に関する事例もございますので、異常検知への機械学習導入をご検討の方はぜひ無料相談をご利用ください。