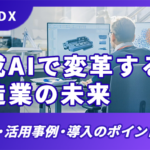
生成AIで変革する製造業の未来|メリットや事例・導入ポイント
2024-09-04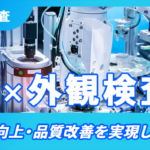
AIによる外観検査|目視検査との違いや成功事例も解説
2024-11-06製造業のDXとは?メリット・ロードマップ・事例を徹底解説
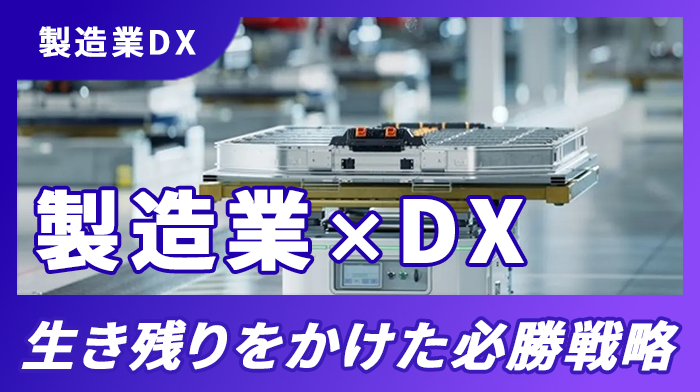
変革期を迎えた製造業において、DX(デジタルトランスフォーメーション)はもはや選択肢ではなく、生き残りをかけた必勝戦略です。
IoT、AI、ビッグデータといった先端技術を駆使し、生産プロセスや業務全体を効率化・自動化することで、生産性や競争力を向上させる製造業DX。
DXを実現できるかどうかが、企業の持続的な成長に大きく影響すると言っても過言ではありません。
本記事では、まず、DXの必要性を明確にし、その導入によって得られるメリットを詳しく解説。その後、戦略的な取り組み方や成功事例、さらにはDX推進の際に直面する課題についても考察し、今後の指針となる情報を提供します。
製造業におけるDXのメリット
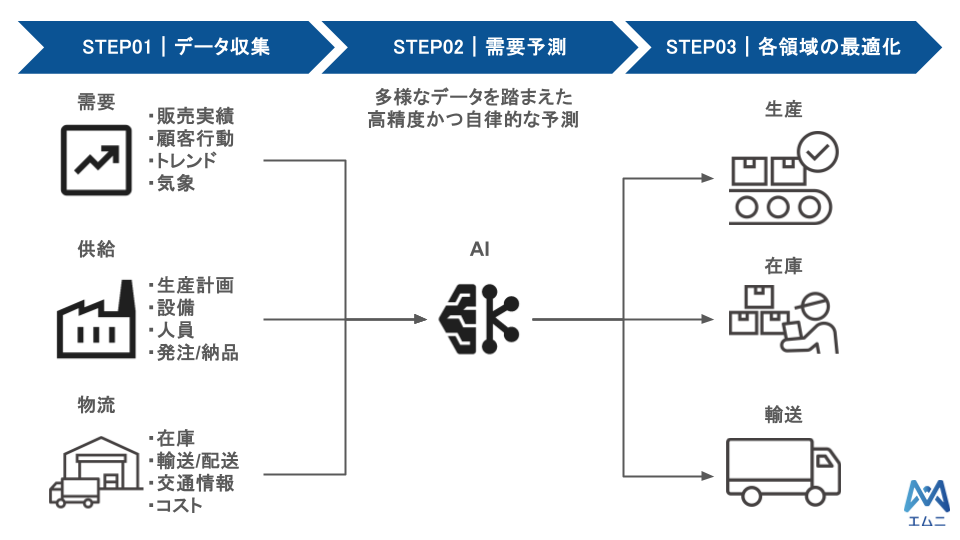
デジタル技術は製造業が直面する課題を解決し、企業の持続的な成長を実現する強力な手段です。DX導入により得られる多くのメリット。これらは企業の未来を切り開くチャンスとなるでしょう。
人材不足への対応
製造業におけるDX導入は、深刻化する人材不足への効果的な解決策として注目されています。特に、IoTやAIといったデジタル技術の活用により、生産プロセスの自動化・省力化が実現され、少ない人員でも高い生産性を維持可能となります。
具体的には、製造ラインの完全自動化や無人搬送車(AGV)による物流自動化、ロボットアームによる組立・検査工程の自動化などにより、スマートファクトリーの実現が進んでいます。また、AIによる外観検査の自動化やセンサーデータを用いた品質予測により、品質管理の高度化も図られています。
労働環境の面では、危険作業や重筋作業のロボット化、遠隔監視・制御の実現により、作業者の安全確保と負担軽減が図られます。これにより、より働きやすい職場環境の構築が進められています。
ただし、導入に際しては段階的な実施と適切な人材育成が重要です。デジタルリテラシーの向上や運用体制の整備を計画的に進め、従業員の理解と協力を得ながら、持続的な改善を図ることが成功の鍵となります。
▼製造業の人手不足について更に詳しく知りたい方はこちら
製造業の人手不足|浮き彫りになる問題とその解決策
属人化の回避
IoTセンサーやデジタルツールによって製造プロセスを数値化・可視化することで、これまで経験則に頼っていた判断基準が明確になります。例えば、熟練工が経験から導き出していた最適な加工条件や検査のポイントをデータとして蓄積することで、誰もが活用できる形式に変換可能です。
さらに、AR(拡張現実)やVR(仮想現実)を用いた作業支援システムにより、未経験者でも高度な技能を要する作業を確実に実施できる環境が整います。
また、従来の紙のマニュアルをタブレットに置き換えることで、作業者は必要な情報をその場で確認できます。画面上で「この部品を、この位置に、この角度で取り付ける」といった具体的な手順を3D映像で見られるため、初心者でも正確な作業が可能になるでしょう。
デジタルツインによるシミュレーションは、ベテラン作業者の暗黙知を形式知に変換する有効なツールとなります。実際の製造ラインをバーチャル空間に再現し、様々な条件下での最適な対応をデータベース化することで、長年の経験に基づく判断プロセスを共有財産として活用できます。
これらのデジタル化により、特定の従業員の不在や退職による生産活動への影響を最小限に抑えることが可能となり、安定した事業継続体制の構築につながります。結果として、製造現場の柔軟性と持続性が向上し、競争力の強化にもつながるのです。
▼属人化の解消について更に詳しく知りたい方はこちら
熟練工の技能伝承を成功させるには|生成AIの恩恵
コスト削減
生産プロセスの自動化により人的ミスが減少し、不良品の発生率が低下することで、材料の無駄遣いや手直し作業に伴うコストを大幅に抑制可能です。
IoTセンサーとAIによるリアルタイムデータの活用は、設備の予防保全を可能にしました。故障の予兆を早期に検知して適切なメンテナンスを実施することで、突発的な設備停止を防ぎ、高額な修理費用や生産ライン停止による機会損失を最小限に抑えることができます。
また、AIを活用した高精度な需要予測は、在庫管理の最適化をもたらします。適正在庫量の維持により、倉庫スペースの効率的な活用が進み、保管コストの削減につながるでしょう。さらに、原材料の発注タイミングを最適化することで、仕入れコストの低減も実現できます。
新たなビジネスモデルの創出
従来の製造業は、製品を作って販売するだけでしたが、製品の使用状況をデジタルデータとして収集し、定期点検や修理などのアフターサービスを提供することで、継続的な収入を得られるようになりました。
例えば、工作機械メーカーが機械の稼働状況を常時監視するサービスを月額制で提供したり、建設機械メーカーが必要な時だけ機械を利用できるレンタルサービスを展開したりする事例が増えています。
また、デジタル技術は顧客一人一人の要望に合わせた製品づくりを可能にします。オンラインで好みのデザインや機能を選べるシステムを導入することで、大量生産品では得られない満足感を顧客に提供できます。
さらに、コンピューター上で製品の設計から動作確認までを行える「デジタルツイン」という技術により、新製品開発の期間とコストを大幅に削減できます。実物を作る前に性能や使い勝手を確認できるため、市場投入までのスピードも格段に向上させることが可能です。
サプライチェーンの強靭化
自然災害の激甚化、新たな感染症の流行、世界各地での国同士の衝突。これらの事象は、部品の供給停止や物流の混乱を引き起こし、生産活動に深刻な影響を与えています。
製造停止のリスクを避けるためにも、サプライチェーンの強靭化は重要な課題であり、DXがその課題解消に大きな役割を果たします。
例えば、工場や倉庫、配送拠点をデジタルでつなぐことで、原材料の在庫が少なくなれば自動的に発注の指示が出されたり、生産ラインの不具合をすぐに検知して対策を講じたりすることが可能です。また、天候や交通状況を踏まえて最適な配送ルートを選択することで、無駄や無理のない製品・部品の配送が可能となるでしょう。
また、AIを活用した需要予測も大きな強みとなります。過去の販売データや市場動向を分析することで、いつ、どの製品がどれだけ必要になるかを高い精度で予測でき、必要な量の製品を適切なタイミングで用意することが可能です。
自然災害や不測の事態が起きても、企業活動への影響を最小限に抑えられる体制が整うでしょう。
顧客満足度の向上
従来の大量生産方式では、画一的な製品しか作れませんでしたが、DXの導入により、個々のお客様の希望に寄り添った製品づくりが可能になります。スマートフォンで手軽に製品のカスタマイズができ、工場では自動でその設計が反映される仕組みが実現できるのです。
また、AIを導入することで、お客様からのお問い合わせに対して、チャットボットが自動対応することも可能です。過去の対応履歴やFAQをもとに、最適な回答を提案する仕組みで、最近では複雑な質問への対応も可能となっています。もしAIで対応できない内容については、担当者に自動で振り分けられるような仕組みも構築するといいでしょう。
また、製品の使用状況や顧客の声をデータとして収集し、AIが分析することで、お客様のニーズを的確に捉えた製品が生まれます。お客様一人一人の声を聞きながら製品を進化させているかのような開発が可能になるのです。
製造業におけるDXの課題
DXは様々なメリットをもたらしますが、その成功にはいくつかの課題を克服する必要があります。DX導入の鍵となるポイントを押さえ、着実にDX導入を推進しましょう。
情報の可視化と共有
製造業のDXを進める上で、大きな壁となっているのが情報の可視化と共有です。
熟練作業者の長年の経験や勘に頼る業務が多く、重要なノウハウが個人の中に埋もれてしまったり、現場では、「あの人でないとわからない」「いつもその人に聞かないといけない」という状況が日常的に発生している場合もあるでしょう。
その対策として、作業データを自動的に収集し、製造ラインの稼働状況や品質データをリアルタイムで共有したり、これまで部門ごとに管理されていた情報を一元化し、必要な人が必要な時に必要な情報にアクセスできる環境を整えることが有効です。
データの可視化ツールを活用すれば、複雑な製造プロセスも一目で理解できるようになるでしょう。グラフやダッシュボードで重要な指標を表示し、問題の早期発見と対応が可能となります。
経営層のリーダーシップとコミットメント
製造業のDXは、組織全体を巻き込む大きな変革です。その成否を左右するのが、経営層の揺るぎない決意と行動力。
経営層に求められるのは、まず自らがDXの本質を理解することです。情報収集しつつも頻繁に製造現場を訪れ、現場責任者とコミュニケーションを取り、DXがもたらす可能性を肌で感じる。そんな姿勢が、全社員の共感を生み出していくでしょう。
加えて、DXの推進には部門の壁を超えた協力が不可欠です。経営層が率先して部門横断のプロジェクトチームを組織し、情報共有とアイデア創出の場を設けることで、組織全体のデジタル化への機運が高まっていきます。
投資判断も重要な要素となります。適切なタイミングでリソースを投入し、専任チームを中心とした推進体制を整えることで、着実な変革を実現できるでしょう。
このように、経営層の強いリーダーシップとコミットメントが、製造業のDXを成功へと導く原動力となるのです。
ITスキルを持つ人材の確保
製造業のDXを進める上で、最大の課題はITスキルを持つ人材の不足。AIやIoT、データ分析など、新しいデジタル技術の知識や経験を持つ従業員が圧倒的に足りていないのが現状です。
特に、熟練工が多い製造現場では、新しい技術への心理的な壁も高いでしょう。長年培ってきた技能とデジタル技術をどう融合させるか、丁寧な教育とサポートが必要となってきます。
この課題を解決するには、オンライン学習や外部セミナーを活用し、段階的にITスキルを習得できる環境を整えることが重要となります。
加えて、即戦力となるITエンジニアを採用することで、DXの推進を加速できるでしょう。リモートワークの活用により、地理的な制約なく優秀な人材を確保することも可能となってきます。
まずはフリーランス人材を採用し、徐々に内製化してスキルを持った正社員を増やしていく、といった戦略も有効な選択肢の一つです。
コスト低減, 投資対効果の明確化
DXは、高額な初期投資に加え、その効果が見えづらいことから、多くの企業が導入を躊躇しているのが現状です。
この課題を解決するには、まず小規模な範囲から着手することが有効でしょう。
特定のラインや工程に限定して試験導入を行い、効果を確認しながら徐々に拡大していくことで、投資リスクを抑えながら確実な成果を積み上げることができます。
効果測定の仕組みも重要となってきます。生産性向上率や不良品率の低減など、具体的なKPIを設定し、定期的に進捗を確認することで、投資効果を数値で示すことが可能となるでしょう。
さらに、外部パートナーとの連携も効果的です。SIerやITベンダーの知見を活用することで、効率的な投資と確実な効果創出を実現できます。
既存システムとの統合
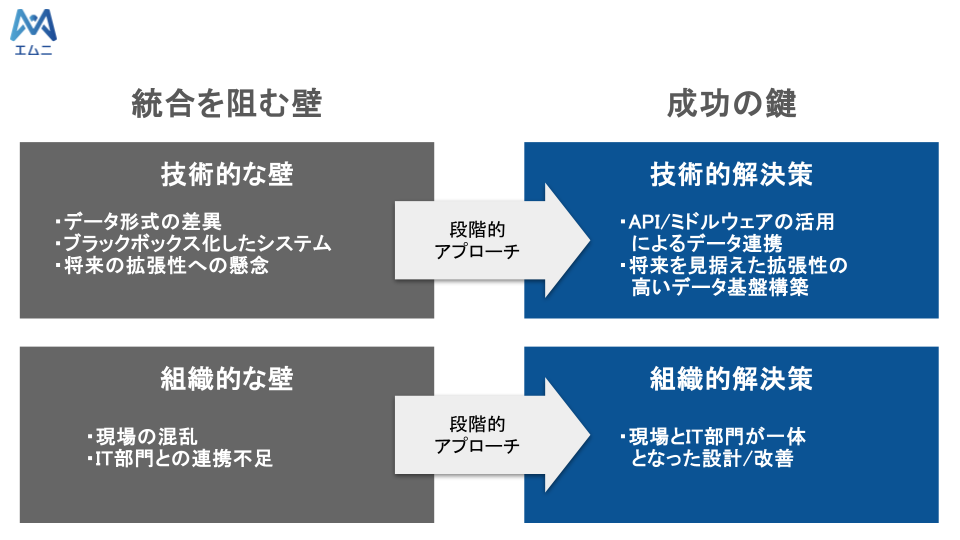
製造業のDX推進において、既存システムとの統合は避けて通れない課題となっています。長年使い続けてきた生産設備や管理システムは、企業の重要な資産である一方、新しいデジタル技術との融合を難しくしているのです。
例えば、20年前のシステムと最新のIoTデバイスをつなげようとしても、データ形式が異なるため直接の連携は困難です。また、古いシステムのプログラムを修正することは、予期せぬ障害を引き起こすリスクも伴います。
この課題を解決するには、段階的なアプローチが有効でしょう。まずは、APIやミドルウェアを活用してシステム間のデータ連携を確立し、徐々に新しい機能を追加していく。このように慎重に進めることで、業務への影響を最小限に抑えることができます。
また、製造現場への導入実績が豊富な外部パートナーの知見も重要となってきます。彼らの経験とノウハウを活用することで、効率的かつ安全な統合を実現できるでしょう。
▼DXの課題について更に詳しく知りたい方はこちら
製造業におけるDXの課題|技術・組織・人材・コストの観点から解説
製造業におけるDX導入のロードマップ
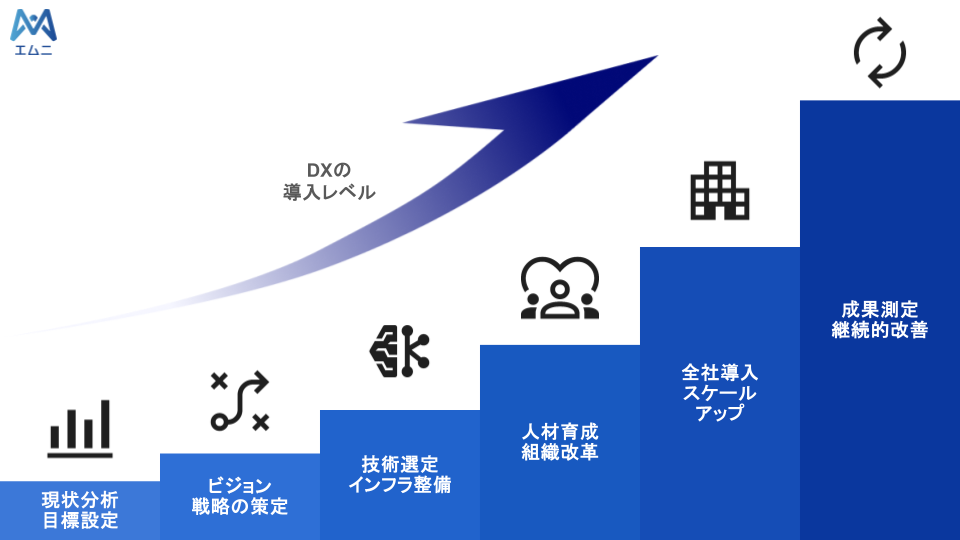
DX導入の鍵となる段階的かつ計画的なアプローチ。以下に説明するような効果的なロードマップを描くことで、貴社へのDX導入を成功に近づけましょう。
現状分析と目標設定
現状分析の第一歩は、業務プロセスの詳細な評価です。製造現場では、作業員の動線や設備の稼働状況、品質管理の方法など、あらゆる業務フローを精査します。手作業に依存している工程や、データの記録・共有が非効率な部分を特定し、デジタル化による改善の余地を見極めるのです。
技術インフラの評価も重要です。既存の生産管理システムや品質管理システムの機能を棚卸しし、新たなデジタル技術との親和性を確認します。データの形式や保管方法、セキュリティ対策なども詳細に調査し、技術的な投資の範囲を明確にするといいでしょう。
人材のスキル評価では、現場作業員からエンジニア、管理職まで、各層のデジタルリテラシーを把握します。IoTデバイスの操作やデータ分析ツールの活用など、新たに必要となるスキルを特定し、教育・研修プログラムの策定につなげることが重要です。
これらの現状分析に基づき、具体的な目標を設定していきます。生産性向上の数値目標や、不良品率の低減目標、リードタイムの短縮目標など、定量的な指標を設定しましょう。また、新規事業の創出や顧客満足度の向上といった定性的な目標も、可能な限り測定可能な形で設定します。
ビジョンと戦略の策定
製造業のDXを成功に導くには、経営層が描く未来像を全社員で共有することが大切です。「3年後、5年後にどんな会社になっていたいのか」。この明確なビジョンが、変革への第一歩となります。
例えば、「IoTとAIを活用して品質管理を革新し、不良品ゼロの工場を実現する」「デジタル技術で熟練工の技能を見える化し、誰もが高品質な製品を作れる企業にする」といった具体的な目標を掲げましょう。
このビジョンを実現するために、段階的な戦略を立てていきます。どの工程から着手し、どのような技術を導入するのか。必要な予算や人材は何か。綿密な計画を立てることで、着実な実行が可能となるでしょう。
大切なのは、全社員を巻き込んでいくことです。現場の意見を積極的に取り入れ、一人一人が主役となってDXを進めていく。そんな風土づくりが、変革を成功に導く鍵となります。
このように、明確なビジョンと実行可能な戦略が、製造業のデジタル変革を確かなものにしていくのです。
技術選定とインフラの整備
製造業のDXで最初に重要となるのが、適切な技術の選定です。ただし、世の中にあふれる最新技術に飛びつくのは危険でしょう。まずは「品質向上」「生産性改善」「コスト削減」など、具体的な課題を明確にすることから始めます。
例えば、品質検査の精度を上げたいのであればAIの画像認識技術が有効です。人の目では見落としがちな微細な欠陥も、24時間休まず検出できます。設備の予防保全なら、IoTセンサーとAIの組み合わせが効果的でしょう。異常の予兆をいち早く察知し、突発的な故障を防ぐことができます。
ただし、こうした技術を活かすには、適切なインフラ整備が不可欠です。例えば、画像認識AIを導入する場合、高解像度カメラの設置場所や撮影条件の検討から始まり、大量の画像データを処理するためのコンピューター環境、そしてデータを保存・分析するためのクラウド基盤まで、一連の整備が必要となります。
設備の予防保全システムでも同様です。IoTセンサーの選定と設置、データを収集・分析するためのネットワーク環境、そして異常を検知した際の通知システムまで、包括的な整備が求められます。
このように、技術選定とインフラ整備は両輪となります。優れた技術も、それを支えるインフラがなければ十分な効果を発揮できません。逆に、充実したインフラも、適切な技術の選定があってこそ、その真価を発揮できるのです。
人材育成と組織改革
DXを成功させるには人材育成と組織改革が非常に重要で、いくら綿密な戦略を練っても、人材や組織がついてこなければ失敗に終わります。
特に鍵を握るのがリーダーの選定です。全社的なDX推進を担うリーダーには、デジタル技術への深い理解と変革への強い意志を持つ人材を選定しましょう。
製造現場の知見とIT技術の両方に精通していることが望ましく、また、部門を超えた調整能力も重要となります。リーダーは経営層と密接に連携し、DX戦略の方向性を明確に示す役割を担います。
また、DX推進チームの編成も重要です。製造、IT、品質管理など、各部門から専門性の高いメンバーを集め、横断的なチームを構築します。チーム内では定期的な進捗確認と課題共有を行い、迅速な意思決定と対応が可能な体制を整えましょう。
人材育成では、階層別の教育プログラムを展開します。現場作業者には基本的なデジタルツールの操作やデータ入力の重要性を理解させ、管理職にはデータ分析やAI活用の知識を習得させます。外部講師を招いた研修やeラーニングの活用も効果的です。
デジタル人材の確保については、データサイエンティストやAIエンジニアなど、専門性の高い人材を外部から登用する一方、社内人材の育成も並行して実施すると良いでしょう。若手従業員には、デジタルスキルを重点的に身につけさせるキャリアパスを用意することも有効です。
また、DXを推進する組織文化の醸成も欠かせません。経営層自らがデジタル技術を積極的に活用し、変革への姿勢を示すことで、全社的な意識改革を促進します。成功事例の共有や表彰制度の導入により、従業員のモチベーション向上も図るといいでしょう。
このように人材育成や組織改革に力を入れることで、自社だけでDXを推進できる場合もあります。しかし、企業の状況によっては、専門人材が不在のためにDX推進に苦戦することもあるでしょう。
その場合は、IT企業やコンサルティング会社との協業により、最新技術の導入やノウハウの獲得を加速させることができます。ただし、過度に外部依存せず、自社の強みを活かした独自のDX戦略を構築することが重要です。
全社的なDX導入とスケールアップ
成功事例を全社へ広げていく段階では、慎重さと大胆さのバランスが重要です。パイロットラインでの成功体験をもとに、各部門の特性に合わせて展開方法を調整していきましょう。
例えば、IoTセンサーの導入では、製造ラインごとの環境の違いに注目します。温度や振動、粉塵など、現場特有の条件を考慮してセンサーの種類や設置場所を選定することで、より正確なデータ収集が可能です。
AIによる分析も、部門の課題に応じてカスタマイズが必要です。品質管理部門では不良品の検出精度向上に、生産管理部門では需要予測の精度向上に重点を置くなど、それぞれの目的に合わせた最適化を進めていくと良いでしょう。
展開スピードも重要な要素となります。急いで全ラインに導入して混乱を招くより、1ラインずつ確実に成果を出していく方が、結果として早い成功につながるでしょう。
このとき、部門を越えた情報共有も欠かせません。ある部門での成功体験や失敗の教訓を全社で共有することで、より効率的な展開を実現できます。
成果測定と継続的改善
成果測定では、生産性向上率や不良品率の低減、納期遵守率、エネルギー効率、顧客満足度などの具体的KPIを設定します。データ収集は自動化し、ダッシュボードで可視化することで、リアルタイムでの進捗管理を行うと良いでしょう。
また、設備投資の回収状況や運用コストの削減効果など、財務面での評価も重要です。
従業員の意識調査も欠かせません。デジタル技術の活用度や業務効率化の実感度、新しい取り組みへの意欲など、定期的なアンケートやヒアリングを実施します。現場の声を改善活動に活かすことで、より効果的なDXの推進が可能です。
改善活動では、評価結果から課題を特定し、改善策を立案・実行します。AIやIoTの最新動向をキャッチアップし、より高度な自動化や分析を実現するだけでなく、システムのアップデートも計画的に実施し、セキュリティ対策や新機能の追加を行います。
人材育成も継続的に行い、新技術に対応するスキルの習得を支援しましょう。ベストプラクティスの共有や部門を越えた知識交換により、組織全体のデジタル成熟度を高めることが重要です。
▼製造業のDXを成功させるステップについて更に詳しく知りたい方はこちら
製造業DXを成功させるための5ステップを解説
▼中小規模製造業でのDX実現について更に詳しく知りたい方はこちら
中小規模製造業 × DX|労働力不足を解消するテクノロジー
製造業におけるDX導入の成功事例
DX導入に成功した企業は生産性向上や新しいビジネスモデルの創出で大きな成果を上げています。国内外の事例から、どのようにデジタル技術を活用して競争力を向上させたのかを具体的に見ていきましょう。
国内の製造業DX事例
熟練者の引退、需要の多様化、そして人手不足といった現場課題に直面する中で、多くの日本企業が「DX」という一手に活路を見出しています。
ダイキン工業
ダイキン工業は、堺製作所臨海工場においてデジタルツインを活用した“目に見える工場”を実現しています。
ライン上に設置されたセンサーやカメラから収集された部品の流れや組み立て、塗装、プレスなどの工程データをリアルタイムに仮想空間へ反映し、過去の稼働状況をAIが分析します。
しかもこの仕組みは、単なるデータの“記録装置”ではなく、将来想定される異常を予測し、問題発生前にアラートを出せる高度なシステムなのです。
実際にこの導入により、2019年度比で30%以上のロス削減を見込んでおり、製造ラインの停止原因への事前対応が可能になりました。
このシステムでは、カメラとセンサーを活用して工程ごとの稼働データを自動でクラウドに取り込み、仮想空間上の各工程にその動きをマッピングします。
その結果、どの工程で停滞が起きているのかがひと目でわかる可視化が行われ、かつ、過去のデータに基づき将来的なボトルネックの予測もできるようになったわけです。
これにより、ラインに異常が発生した際に人的な判断を待つことなく、システムが即時に対応策を示すという、まさにスマートな生産管理が可能になりました。
さらに注目すべきは、これが内製開発というかたちで進められたことです。
自社で育成したDX人材が主導し、現場の作業者や工程管理者と密に連携しながら開発を進めており、現場の微妙なニュアンスを反映しつつ、現場リーダーが納得する形で仕組みを設計しています。
このように、テクノロジーが現場の課題と真摯に向き合うことで、現場主導の改善が自然に実現されているのです。
この導入によって、“止まらない工場”が生まれました。つまり、単に効率化を図るだけでなく、トラブルの芽を摘み取り、タイムリーに品質を守る仕組みが整ったのです。
旭化成株式会社
旭化成株式会社では、自社と競合他社の特許情報をテキストマイニングによって深く解析する仕組みを構築しています。
大量の特許出願や登録情報を自然言語処理で分析し、似た技術どうしをマッピングすることで技術分野を“見える化”することが可能です。
その結果として、どの分野で自社が優位に立っているのか、また競合との差別化ポイントがどこかが明確になりました。
この分析手法は特許だけでなく、事業戦略にも直結します。たとえば、スパンボンド不織布事業においては、他社との技術重複や連携可能性を客観的に明示し、共同事業会社設立の意思決定に活用された実績があります。
将来性のある技術領域をいち早く特定し、新規事業の創出や、M&A案件の検討材料にもなるため、DX的な知財戦略の最前線を行く取り組みと呼べるでしょう。
さらに最近では、生成AIを活用して、特許文書の作成・検索といった知財業務自体の効率化が進んでいます。
旭化成では文書作成・検索で月間2,000時間、監査対応で年間1,800時間以上の工数削減成果をすでに実現しているとの報告もあり、知財業務の高度化と省力化を同時に推進しているようです。
▼特許調査を効率化する方法について更に詳しく知りたい方はこちら
AIで特許調査のコストを1000分の1に|活用戦略を詳しく解説
このような取り組みからは、テキストマイニングによる可視化だけにとどまらず、生成AIを組み合わせて、知財部門の本質的価値向上を目指す姿勢が読み取れます。
分析によって導かれた技術インサイトを経営判断に活かし、効率化された業務体制がさらなる戦略的領域への注力を可能にしているのです。
結果として旭化成では、特許という知的財産を事業ポートフォリオに組み込み、価値最大化サイクルを回している状況にあります。
トヨタ自動車九州株式会社
トヨタ自動車九州では、これまで熟練工の経験や感覚に頼っていた不良予兆の検出を、AIと人の協働によって自動化する画期的なシステムを導入しています。
プレス工程で鋼板に圧力を加えてパネルを成形する際、従来は熟練工が目視感覚を頼りに微細な形状のズレを見抜いていました。
しかし、このシステムではプレス機内部に設置されたサーモカメラが連続的にパネルを撮影し、AIがその熱画像を解析することで、ミリ単位の膨張や縮小といったわずかな差異を高精度で検出します。
この解析には、トライアートの「4CAS(for Cognition And Sensitivity)」と呼ばれるコンポジットAI技術が採用されており、まず基準となる“マスター画像”を生成し、その後に生成されたマスターと現行のパネルとのズレを連続的に評価するという仕組みになっています。
5秒に1枚作られるすべてのパネルをAIが評価する体制を整えたことで、従来なら熟練工にしか分からなかった“不良予兆の法則性”を数値化し、検出精度の飛躍的な向上を実現しました。
さらに特徴的なのは、このシステムが完全自動ではなく、人とAIの協働によって設計されているという点です。
画像生成段階ではAIの判断に加えて現場作業員による形状指定がフィードバックされ、その後にAIによる再演算が行われるというハイブリッドなワークフローが採用されているのです。
この手法によって、AIが全自動で判断しにくいケースにも人の経験が活き、ブラックボックス化せず、現場に根ざした運用が可能となっています。
このシステム導入によって、熟練工の暗黙知による検査が形式知へと転換され、技能の汎用化が進みました。
また、人手だけでは検知が難しかった超微小なズレも見逃すことなく捉えるため、不良を未然に防ぎ、品質と生産性の両立を可能にしています。
▼暗黙知を形式知化するプロセスについて詳しく知りたい方はこちら
生成AIで暗黙知を形式知化するメリットやプロセスを解説
三菱電機株式会社
三菱電機株式会社は、「e‑F@ctory(イーファクトリー)」と呼ばれる「生産情報とITを一体化する仕組み」を導入しています。
これは単なるIoT導入ではなく、工場にある装置や生産ラインからリアルタイムにデータを収集し、その場で処理して現場へフィードバックするエッジコンピューティングを組み込むことで、いわば“現場とITのつながりを常時維持するシステム”です。
これにより、トレーサビリティや異常の早期発見、さらには予防保全までを視野に入れたスマートな生産管理が可能になります。
さらにe‑F@ctoryは、SCADAやシミュレータ、クラウド分析と連携することで、設備レベルを超えたエンジニアリングチェーンとサプライチェーンの俯瞰的な可視化を実現しています。
たとえば、GENESIS64による監視制御や3DシミュレータMELSOFT Geminiを用いた制御検証、データサイエンスツールMaiLabによる大量データ解析などを組み合わせ、ものづくり全体としての生産性改善やコスト最適化を狙っています。
e‑F@ctoryは2003年の概念提唱から始まり、2011年には企業やパートナー企業を巻き込む「e‑F@ctory Alliance」へと進化しました。
現在では世界中で400〜600社規模の企業が参画し、Edgecrossコンソーシアムなどのオープン標準化にも貢献。
こうして実際に、名古屋製作所などではサーボモータ工場の不良率低減や品質向上、生産性向上が実現され、不良率が10分の1に減少、生産性が180%に向上した実績もあります。
また、2011年以降は省エネにも展開し、工場内消費エネルギーを25%削減した報告もあります。
このように三菱電機のe‑F@ctoryは、ただ設備をつなげて情報を集めるだけでなく、エッジで“即時の判断”、ITで“全体最適”、パートナー連携で“柔軟なソリューション開発”を可能にする非常に強力なプラットフォームです。
工場単位にとどまらず、サプライチェーンや設計工程までを巻き込む総合的な改善サイクルを構築しています。
海外の製造業DX事例
海外の製造業でも、デジタルを活用して顧客体験と業務効率の飛躍的な向上を実現しています。
BMW社
BMWは自動車工場全体を3Dモデルとしてデジタル上に再現し、「仮想工場」としてシミュレーションを行っています。
NVIDIAのOmniverseプラットフォームを活用することで、完成前の装置配置や人やロボットの動きを仮想空間上で試行でき、設置後に発覚しやすい干渉や工程ミスを事前に発見することが可能です。
また、ライン設計の段階で物理的な試行錯誤を大幅に削減したため、設計期間やコストを効率化し、導入速度も向上したと考えられます。
さらにBMWは現在、31以上の工場を同一プラットフォーム上で仮想化し、全工場を横断的に管理する体制を構築しています。
これにより新モデル投入時には、数週間かかっていた物理試験をわずか数日で完了できるようになりました。
例えばライン内を車体模型で物理的に試す必要があった工程は、仮想空間での衝突チェックに置き換わり、時間とコストの両面で約30%の効率化が実現しています。
加えて、人が動く姿の3Dシミュレーションにも対応しており、VRを使った業務確認や教育にも活用されているようです。
これまで人や現場の経験や勘に頼っていた工程管理が、仮想空間での検証とAIによる最適化に支えられることで、理論と実践が融合したスマートなものづくりへと進化しています。
今後は生成AIが工程改善の提案やロボット動作学習を担うなど、デジタルツインとAIの連携がさらに深まっていくことでしょう。
CEMEX社
CEMEX社が開発した「CEMEX Go」は、生コンクリートの発注から出荷、配送追跡、支払い、取引履歴の管理までを一括で行えるデジタルプラットフォームです。
この仕組みによって発注作業や発送状況の確認、履歴照会といった従来時間のかかっていた業務が、瞬時に完了するようになりました。
CEMEX社のグローバルな顧客のうち、現在は約6万社がこのプラットフォームを利用しており、グループ全体の受注の60%がこのシステム経由で処理されているほどです。
さらに、チャットボット「Olivia」が導入されており、60以上のFAQに対応して多言語で24時間体制の顧客対応が可能になっています。
これにより顧客満足度の向上はもちろん、営業担当者がより付加価値の高い仕事に集中できる環境が整ったのです。
CEMEX社はこのプラットフォームによって、顧客とのエンゲージメントを強化し、効率と競争力の両方を高めることができています。
BASF社
BASF社が開発した「AUROOM®」は、自動車外装色の3D CADプラットフォームで、デザイナーが物理サンプルを待つことなくフォトリアルな色の光沢や「フロップ(色の変化)」、スパークリング効果をどの角度からでも確認できる環境を提供しています。
カメラで撮影された600以上の自動車塗料のデジタルカラーが高精度の数学モデルと色彩計測技術によって処理され、OEMメーカーは初期設計段階において完成車の色味をリアルに検証できるようになりました。
このプラットフォームによって、従来は試作パネルの塗装と輸送に数日を要していたプロセスが、設計検証を数日早めるだけでなく、意思決定のスピードと精度も飛躍的に改善されています。
色の比較やコメント機能も備えており、関係者間でのコミュニケーションが円滑になることで、無駄な試行錯誤を減らすことに役立っているのです。
さらにAUROOM®は、BASFが開発したAUVOTと呼ばれる仮想3D車両モデルにも対応しており、ダッシュラインや曲面部など色の効果が変わりやすい部分も忠実に再現されます。
この組み合わせによって、OEMは量産前の設計段階で品質を確保しやすくなり、開発コスト削減と高速化が両立できているでしょう。
このようにAUROOM®は単なるデジタル化にとどまらず、塗料販売から一歩進んで「価値ある体験」へとビジネスモデルを大きく変革した事例といえます。
製造業におけるDX導入の注意点
DX導入における様々な注意点。以下に示すポイントに気を付けながらDXを推進することで、その効果は最大化されます。具体的な注意点を確認していきましょう。
データセキュリティとプライバシー
製造業のDXを進める中で、データセキュリティの確保は最優先課題となっています。IoTセンサーの設置やクラウドシステムの活用により、膨大なデータがネットワーク上を行き交うようになった今、情報漏洩やサイバー攻撃のリスクは日々高まっているのです。
特に注意が必要なのは、製造現場の機密情報です。
例えば、温度や圧力の微妙な制御方法、材料の配合比率、検査時の判定基準など、現場で磨き上げてきた技術的なノウハウは、デジタル化によってより体系的に管理できるようになる反面、データとして扱われることで、漏洩のリスクも高まってくるのです。
取引先との機密情報も要注意です。新製品の開発情報、生産計画、価格交渉の内容など、取引先との信頼関係に関わる重要なデータも、適切な保護が必要となります。
こうした機密データは、重要度に応じて段階的な保護措置を講じることが有効です。最重要データはオンプレミス環境で厳重に管理し、比較的重要度の低いものはクラウドで運用するなど、柔軟な使い分けが求められるでしょう。また、クラウドに保存する情報は全て暗号化し、アクセス権限を厳密に管理することも重要です。
これらの技術的な対策だけでなく、従業員教育も重要な要素となります。最新のセキュリティ対策も、使用する人の意識が低ければ意味がありません。定期的な研修を通じて、全社員のセキュリティ意識を高めていく必要があります。
長期的な視点を持つ
製造業のDXは、長期的な視点で取り組むべき重要な経営課題です。確かに、初期投資は大きく、その効果が目に見える形で表れるまでには時間がかかりますが、目先の利益だけを追い求めていては、真の競争力強化は望めません。
DXによる変革は、組織の在り方そのものを変えていく取り組みです。データに基づく意思決定の文化を醸成し、従業員一人一人のデジタルスキルを高め、新しい価値創造の仕組みを作り上げていく。そのためには、3年、5年といった中長期的な視点が欠かせません。
技術の進化も重要な考慮点となります。現代社会の変化の激しさを考慮すると、今の最新技術も数年後には陳腐化している可能性が高いでしょう。そのため、将来の技術動向を見据えながら、柔軟に対応できる体制を整えることが重要となります。
投資計画についても、最初から全社的な大規模投資を行うのではなく、小規模な実証実験から始めて効果を確認し、徐々に展開を広げていく。こうした慎重なアプローチが、確実な成功につながっていくのです。
まとめ:DXはもはや選択肢ではなく、生き残りをかけた必勝戦略
製造業におけるDXは、もはや一部の先進企業だけのものではありません。生産効率の向上や単純なコスト削減を超えて、企業の存続そのものを左右する重要な経営課題となっています。その中核を担うのが、AIの活用です。
しかし、多くの企業が「AIをどう活用すればよいのか」「本当に効果が得られるのか」といった不安を抱えているのも事実です。コストやリソースの問題、適切な技術の選定など、AI導入には様々な課題がついて回ります。
そのようなお悩みに応えるため、エムニでは無料相談を実施しています。例えば品質検査の自動化、設備の予防保全、需要予測の高精度化など、お客様の具体的な課題に対して、最適なAIソリューションをご提案いたします。
相談では、まず貴社の製造現場が抱える課題や現状をじっくりとお伺いします。そして、類似の製造業での豊富な導入実績をもとに、期待できる効果や必要な投資、導入までのステップを分かりやすくご説明し、「まずは小規模な実証実験から始めたい」「段階的に投資を検討したい」といったご要望にも柔軟に対応いたします。
また、AIの技術選定やシステム構築だけでなく、現場への導入支援や運用サポートまで、製造業のAI活用を一貫してサポート。貴社の状況に合わせた最適なアプローチをご提案いたします。
まずはぜひ気軽にご相談ください。