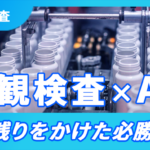
目視による外観検査の問題点と生成AIによる解決策を徹底解説
2024-11-26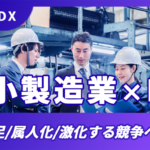
中小規模製造業 × DX|労働力不足を解消するテクノロジー
2024-11-29生産計画にAIを使うメリットとは?活用事例5選!
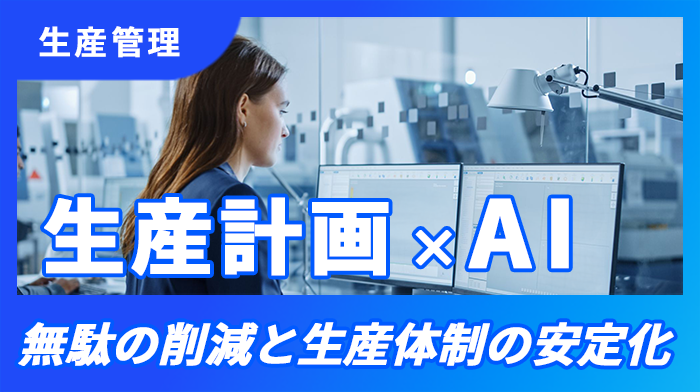
日本の製造業は、少子高齢化による人材不足、デジタル化の遅れ、不安定なサプライチェーンなど、様々な問題を抱えています。こうした問題を解決し、競争力を保つためには、AIの活用が欠かせません。
AI技術は近年急速に進歩し、生産計画や在庫管理、品質管理といった分野においても導入が進んでいます。また、2024年現在、持続可能性を意識したAIの活用にも注目が集まっており、今こそAI導入の絶好のタイミングといえるでしょう。
この記事では、製造業が抱える現状やAI導入によって生産計画に期待できるメリット、具体的な活用事例、さらに導入を成功に導くためのポイントについて、わかりやすく解説いたします。
生産計画におけるAI活用の3つのメリット
製造業において、生産計画にAIを導入することは、業務の効率化や精度の向上、さらには新たな価値の創出へとつながる重要な手段です。
需要予測の精度向上と在庫の最適化
AIを活用した高度なデータ分析により、消費者の購買行動や地域ごとの需要変動など、複数の要因を迅速に処理し、精度の高い需要予測が実現可能です。このため、製造業は需要に基づいた適正な生産量を確保し、余剰在庫や欠品のリスクを抑えることができるでしょう。
さらに、AIによる需要予測の精度向上は、在庫管理の効率化にも貢献しています。適切な在庫量を確保することで、倉庫スペースの有効活用や無駄のない資源管理が実現し、コスト削減へとつながるのです。この結果、経営効率の向上が期待され、販売機会の最大化にも寄与します。
生産計画の自動化
従来、経験や勘に頼って立てていた生産スケジュールも、AIによる自動化により、生産計画の精度が大幅に向上しています。AIは過去データやリアルタイム情報を基にリソースを最適に活用し、無駄な稼働の削減と安定した生産体制の確立を可能とするのです。
さらに、AIによる生産計画の自動化は、柔軟性の向上にも寄与します。需要の変動や突発的なイベントにも迅速に対応し、計画を柔軟に調整できるため、顧客への安定供給が維持されるでしょう。加えて、単調な業務をAIに任せることで、担当者はより創造的な業務に集中でき、結果として企業の競争力を高めることが期待されます。
不良品削減と品質管理の強化
AIを活用した画像認識技術により、生産ライン上での不良品検出が大幅に強化されます。高精度カメラで捉えた画像をAIが解析し、製品の微細な欠陥を即座に検知することで、不良品が市場に出回るリスクを抑え、品質の安定化が図れます。
また、AIで収集された品質データを分析することで、不良品発生の根本原因を迅速に特定し、改善施策をすぐに講じることが可能です。このデータは製品改良や工程の最適化に活用され、長期的な不良削減と生産効率の向上が期待できます。結果として、顧客の期待に応えられる高品質な製品を安定的に提供する体制が実現するでしょう。
日本の製造業の問題点と解決策
日本の製造業は現在、少子高齢化による人材不足や、デジタル化の遅れ、サプライチェーンの分断リスクなど、さまざまな問題に直面しています。
人材不足と高齢化
日本の製造業では、少子高齢化により若い労働力が減少し、技術継承が難しくなるという深刻な問題に直面しています。特に34歳以下の若年層が減少する中、経験が求められる技術やノウハウが現場で不足し、生産性の低下を引き起こしているのが現状です。この傾向は国際競争力にも影響を与えかねず、対策が急務と言えるでしょう。
こうした状況を打破するためには、人材の育成と確保が最優先課題となります。さらに、技術の継承を補う手段として、デジタル技術やAIを活用した業務の効率化や自動化を進めることも重要です。
自動化とデジタル化の遅れ
日本の製造業では、諸外国と比べてデジタルトランスフォーメーション(DX)や自動化の普及が遅れています。生産性を高めるためには、AIを活用したDX推進が不可欠です。特に、生産計画にAIを導入することで、需要予測や在庫管理、ライン稼働率の最適化など、データに基づく精密な意思決定が可能になります。
こうしたAI導入には経営層がその効果を正しく理解し、評価することが重要です。さらに、既存システムとの統合に伴う課題を解決することで、効率化や競争力向上、安定した事業運営への道が開けるでしょう。
サプライチェーンの分断リスク
サプライチェーンの分断は、企業が考慮しなければならない重要なリスクの一つです。しかし地政学的な緊張や自然災害によって、サプライチェーンが寸断されるリスクはますます高まっています。
米中対立やロシアのウクライナ侵攻により、貿易制限が強化され、多くの企業に異なる地域向けの複数のサプライチェーン構築が求められている状況です。また、気候変動による異常気象が頻発し、自然災害による物流網の寸断リスクも増大しています。
こうしたリスクに備えるため、企業にはサプライチェーンの分散や多様化が求められるでしょう。また、事業継続計画(BCP)を策定し、供給網の柔軟性を確保することも重要です。さらに、AIやデータ分析を導入し、リアルタイムで供給状況を監視する体制を整えることで、安定的な生産活動を支える仕組みが構築されます。
生産計画における課題
製造業における生産計画では、品質やヒューマンエラーに関する課題が存在します。
標準化を行い品質を安定させる
製造業における品質安定を達成するには、体系的な標準化の推進が不可欠です。
まず、作業手順の徹底的な標準化から着手します。各工程における作業内容を細分化し、具体的な手順を明文化することが大切です。特に品質に影響を与える重要工程については、作業のポイントと管理基準を明確に定義します。
次に、測定方法や判定基準を標準化し、検査項目ごとに詳細な基準値を設定して、合否判定の客観性を高めます。また、作業環境の標準化も重要です。温度、湿度、照明などの環境条件が品質に与える影響を考慮し、適切な管理基準を設定します。作業場所のレイアウトや器具の配置まで含めて標準化することで、作業効率と品質の両立を図るといいでしょう。
これらの標準化により、工程間や工場間での品質のばらつきを低減し、安定した品質レベルの維持が可能となります。標準化は一度で完成するものではなく、現場からのフィードバックを基に継続的に改善を重ねることが、真の品質安定化につながります。
ヒューマンエラーを防止する
入力ミスや誤発注といったヒューマンエラーは、生産スケジュール全体に遅れやズレを引き起こす要因になり得ます。
例えば、作業担当者が生産予定数を誤って入力した場合、追加の発注が必要となり、計画変更の負担が発生することもあるでしょう。また、エラーを防ぐために確認作業が増えれば、時間や人員のコストがかさみ、全体の効率が低下する可能性があるのです。
こうしたヒューマンエラーを最小限に抑え、効率を高めるための方法として、自動化システムやデジタルチェック機能の導入が有効です。これにより、入力ミスを減らし、確認作業の負担も軽減されます。
さらに、デジタル化によって作業の正確性が向上し、生産スケジュールの安定化にもつながります。このような改善策を取り入れることで、より効率的でミスの少ない生産環境の実現ができ、全体のパフォーマンス向上も見込まれるでしょう。
日本の製造業におけるAI導入の現状
過去、日本の製造業におけるAI技術の導入は慎重に進められてきました。2010年代後半から2020年代初頭にかけて、多くの企業がAIを試験的に取り入れ、生産ラインで実験的に活用する流れが見られたのです。
この段階での主な取り組みは、AIによる需要予測や品質管理の効率化であり、データ解析や一部の自動化に役立てることが中心でした。しかし、技術の進展と企業の理解が深まるにつれ、製造業全体におけるAIの活用が広がる可能性が見出され、政府の産業支援も追い風となったのです。
現在、2018年から始まったAI導入の取り組みが成果を上げつつあり、リアルタイムでのデータ分析や高度な自動化が可能な「スマートファクトリー」の整備が進んでいます。
特に、労働力不足や生産性の課題解決に向けて、AIとIoTを組み合わせた生産システムが構築され、製造業の効率化と柔軟な対応力が大幅に向上しました。
2024年の現在、日本の製造業はグローバル競争力の向上や持続可能性の実現を目指し、AIのさらなる高度活用に積極的に取り組む重要な局面を迎えています。政策支援や技術基盤も整い、AI導入を検討する企業にとっては絶好のタイミングと言えるでしょう。
生産計画におけるAI活用事例 5選
生産計画にAIを導入することで、製造業は効率化や最適化を実現し、競争力を大幅に高めることができます。ここでは、日本の代表的な製造業企業がどのようにAIを活用し、生産計画を改善したのかを具体的に紹介します。
Siemens(シーメンス)
Siemensはドイツに本社を置く総合電機メーカーで、製造業向けのインフラや産業オートメーションに強みを持つ企業です。
Siemensは、AIの活用によってメンテナンスの効率化と品質管理の向上を実現しています。予測メンテナンスにより、部品が故障する前に交換のタイミングを見極め、計画外の長期停止を防止。これにより、生産損失のリスクを抑えているのです。
また、規範的メンテナンスでは、AIが複雑な機械の動作を最適化し、必要な修理部品の事前準備もサポートしています。
品質管理においても、SiemensはAIを活用し、生産データを駆使することでプリント回路基板の検査回数を30%削減。これによりスループットの向上も実現しています。
さらに、AIによって欠陥の原因を特定し、品質のさらなる向上を目指すことで、製造現場の信頼性と効率性の大幅な強化を進めているのです。
参考記事:Four AI case study successes in industrial manufacturing | Control Engineering
キッコーマン
キッコーマンでは、約2000種類におよぶ商品の需要予測の精度向上と、生産計画の効率的な管理が求められている状況でした。従来、需給担当者が経験に基づき手作業で予測を行っていたため、多数のアイテムを担当することで特にピーク時には業務負荷が増大していました。
AI需要予測システムを導入したことで、迅速かつ正確な需要予測が可能となり、生産計画の最適化が実現。さらに、このシステムは簡単な操作で高精度な予測を行えるだけでなく、大量のデータを短時間で処理するパフォーマンスを備えています。これにより、業務時間の大幅な短縮と効率的な生産体制の確保が可能になりました。
この結果、キッコーマンは需要と供給のバランスを保ちながら、在庫管理や生産調整の効率化を達成し、安定した商品供給を実現できたのです。
参考記事: キッコーマン株式会社 様:日立ソリューションズ東日本
トヨタ自動車
トヨタ自動車の素形材技術部では、これまで検査工程を熟練技術者が目視で担当しており、作業が個人の技量に依存しやすく、省人化が進みにくい状況にありました。
また、生産量に応じたラインの柔軟な調整が難しく、変動する稼働率に合わせた効率的な運営が求められていたのです。さらに、目視検査では不良箇所をすべて検出することが難しく、検査精度の向上も喫緊の課題となっていました。
こうした課題の解決を図るため、AI画像検査システムを導入し、検査工程の自動化を推進。これにより、自動検査装置によって目視検査の必要がなくなり、熟練技術者に依存することなく、安定して高品質な製品の提供が可能となる体制が整ったのです。また、省人化も実現することができました。
さらに、AIによる検査によって見逃し率0%、過検出率5%という高い精度が達成され、インラインでの抜き取り検査においても不良品の完全な検出が可能であることが確認されました。
完全自動化により、生産ラインの稼働率に応じたライン速度の柔軟な調整が可能になり、人による作業が不要になったことで、待機時間の問題も解消。これにより、生産量の変動に対応した効率的なライン運営が実現しています。
このようにして、トヨタはAI画像検査システムの導入により、複数の課題が解決され、効率的かつ精度の高い生産体制が構築されました。
参考記事:トヨタ自動車株式会社 様 | WiseImaging | 導入事例 | シーイーシー VR+R
花王
花王では、生産プロセスの効率化や品質管理にかかる手間、そしてコスト削減が大きな課題となっていました。さらに、需要予測の精度が低いために在庫管理が非効率であり、トラブル対応や技術継承に関しても課題が残っていたのです。
こうした課題を解決するため、花王はAIとデータ活用基盤の導入に踏み切り、工場に蓄積された約300万件の「現場ナレッジ」データを高度化する取り組みを開始しました。
この取り組みにより、トラブル対応のためのナレッジデータベースと設備保全の管理システムがクラウドと連携され、迅速な検索と問題解決が可能な体制が整いました。これにより、生産現場での対応速度が向上したのです。
結果として、生産プロセスの自動化が進むと同時に、品質管理の効率化も実現。不良品の発生率が低下し、コスト削減にも貢献する成果を上げました。また、AIによる需要予測の精度向上が生産計画の最適化を後押しし、在庫管理の効率も大幅に改善されています。
このように、花王はAIと最新のデジタル技術を駆使して現場のナレッジを組織全体で共有・活用する基盤を構築し、生産効率の向上と品質改善を達成しました。
参考記事:Azure Cognitive Search をデータ活用基盤に採用した花王
パナソニック
パナソニックでは、生産ラインにおける人手不足や作業効率の低下、新製品の市場投入までの時間短縮が大きな課題として浮上していました。こうした問題に対応するため、AIを活用したロボット技術と生成AIの導入が進められ、次のような効果が得られています。
まずAI技術による生産ラインの自動化を通じて、人手不足が緩和され、作業効率も著しく向上しました。
さらに、生成AIを活用したデータ分析により、製品開発サイクルが短縮され、新製品の市場投入までの期間が大幅に削減されています。このAI技術の導入を通じ、現場の効率化と生産性向上が実現し、業務全体のパフォーマンス改善につながりました。
このように、AIは生産計画の精度向上や業務効率化に貢献し、製造業全体の競争力を強化する重要な手段となっています。
特に、人手不足や熟練技術者の高齢化などの課題に対して、AIによる自動化とデータ分析は有効な解決策となり得ます。企業は、自社のニーズに合わせたAIの導入を進めることで、さらなる成長と競争力の強化を図ることが可能です。
参考記事:パナソニック コネクト 生成AI導入1年の実績と今後の活用構想 | 技術・研究開発
生産計画におけるAI導入で失敗を防ぐための重要なポイント
AI技術の進展に伴い、製造業における生産計画にAIを活用する動きが活発化しています。しかし、AIの導入には十分な準備と適切な管理が不可欠です。
経営層が的確な判断を行えば、導入に伴うリスクを軽減し、最大限の効果を引き出すことができるでしょう。ここでは、生産計画にAIを導入する際に失敗を防ぐための重要なポイントについて、わかりやすく解説します。
明確な計画と準備
AI導入を成功させるためには、導入の目的や期待する成果を明確に設定し、具体的な計画を立てることが重要です。
まずは、どのプロセスを自動化するのか、どのような業務改善を期待するのかを経営層が明確に理解する必要があります。また、現状の業務プロセスを詳細に分析し、AIがどのように役立つのかを具体的に把握しておくことが重要です。
例えば、生産計画のどの部分にAIを活用するか(需要予測、スケジューリング、在庫管理など)を明確にすることで、AIが組織全体にどのような影響を与えるかを把握できます。
従業員への教育とトレーニング
AIシステムを効果的に運用するためには、従業員の理解と協力が欠かせません。新しい技術を最大限に活用するには、操作方法の理解だけでなく、データ分析やAIの基本的な概念に対する知識も重要です。
特に、生産計画に携わる担当者や、AI導入によって日常業務に影響を受ける従業員には、データサイエンスや機械学習の基礎を学んでもらうことで、AI導入後の適応がスムーズに進むでしょう。
教育とトレーニングを通じて、従業員が新しいシステムに抵抗なく対応できる環境を整えることが、AI導入の成功には欠かせない要素となります。
データセキュリティの確保
AIシステムは大量のデータを取り扱うため、データセキュリティの確保は極めて重要です。適切なセキュリティプロトコルを導入し、データの漏洩や不正アクセスから組織を守る対策を講じることが求められます。
特に、個人情報や企業の機密情報を含むデータには細心の注意を払い、安全性の高い環境での管理が必要です。
セキュリティ対策が不十分なままAIを導入すると、情報漏洩やサイバー攻撃によるリスクが発生し、企業の信頼を損ねる可能性があります。AIを運用するインフラ全体のセキュリティを強化し、安全な運用環境を確立することが不可欠です。
段階的な導入によるクイックウィンの獲得
AI導入を成功させるには、一度に全てを変革するのではなく、段階的に進めることが重要です。
まずは小規模なプロジェクトから始め、効果を確認しながら次のステップに進む「スモールスタート」戦略を採用することで、導入リスクを最小限に抑え、社内への導入がスムーズに進みます。
例えば、生産ラインや在庫管理の一部にAIを導入し、成果と課題を評価し改善を重ねることで、全社的な導入がよりスムーズに進むでしょう。
専門人材のサポートを得る
AIを効果的に活用するためには、適切な知識とスキルを持った人材の協力が重要です。AI導入に伴い、従業員が新しいスキルを学び、技術力を高められるのも大きなメリットとなります。
また、AIの導入が初めての企業にとっては、外部の専門パートナーやコンサルタントのサポートを得ることが効果的です。
専門知識を持つ外部の協力を受けることで、導入プロセスがスムーズに進み、トラブルシューティングや導入後の最適化も効率的に行えます。
また、長期的な運用やメンテナンスにおいても、信頼できるパートナーの支援があることで、社内リソースにかかる負担を軽減し、安定したAI活用環境を構築することが可能です。
まとめ :日本の製造業がAIで進化する, 生産計画効率化と競争力強化への道筋
AIの戦略的活用により、日本の製造業は新たなステージへ進化します。生産計画の精度向上とコスト削減を同時に実現し、グローバル競争力を強化できます。さらに、データ駆動型の意思決定により、品質管理の高度化と柔軟な生産体制の構築が可能です。
一方で、成功への道のりには綿密な準備と実行が不可欠です。経営層による明確なビジョン設定、段階的な導入計画、従業員教育の充実、そしてデータセキュリティの確保など、取り組むべき課題は少なくありません。
弊社は製造業に特化したAI導入支援と継続的なサポートを提供しています。DX推進による競争力強化をご検討の際は、まずは無料相談でお気軽にご相談ください。豊富な導入実績を基に、御社に最適なソリューションをご提案します。