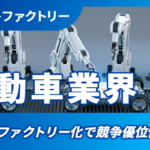
自動車業界のスマートファクトリー化|メリットや事例
2024-11-17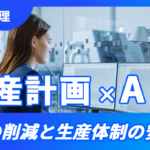
生産計画にAIを使うメリットとは?活用事例5選!
2024-11-27目視による外観検査の問題点と生成AIによる解決策を徹底解説
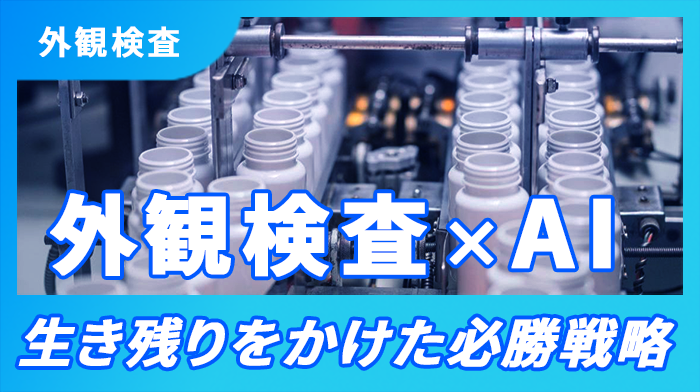
製品の品質に直結し、妥協が許されない「外観検査」。
しかし、人が目視で検査することによる「主観による品質のばらつき」や「見逃しなどの人的ミス」が深刻な問題となっています。安定した高品質な製品の供給を実現するには、新たなアプローチが必要となるでしょう。
そこでこの記事では、目視で行う外観検査の現状と抱える課題について触れ、それらを改善するための具体的な方法について解説していきます。外観検査の理解を深めるとともに、最新技術や手法を効果的に組み合わせることで、品質管理体制を強化し、企業としての競争力向上を目指しましょう。
外観検査の高度化を実現するためにもぜひ参考にしてください。
目視による外観検査(目視検査)とは
目視検査とは、人間の五感、特に視覚を使って製品の品質や状態を直接確認する検査方法を指します。形状や色、サイズ、表面の状態、異物混入など、さまざまな項目を目視でチェックすることで、不良や異常を見つけ出すことが可能です。
目視検査の目的:製品の品質と安全性を支える
目視検査は、製造現場で製品の品質を守るための基本的な工程の一つです。製品の表面に傷や汚れがないかを確認するだけでなく、品質管理の中でも重要な役割を果たしており、検査自体にはより深い目的と意義があります。
製品の信頼性向上
人間の目は、最新の機械やAIでも捉えきれない繊細な変化や異常を検出できるため、製品の信頼性確保において、目視検査は極めて重要な役割を担っています。
例えば、製品表面の微妙な色むらや光沢の違い、わずかな凹凸、微細な傷など、数値化が難しい品質特性を瞬時に判断することが可能です。これらの一見些細な欠陥も、製品の使用過程で深刻な問題に発展する可能性があります。傷は製品の強度低下につながり、色むらは内部構造の不均一性を示唆している可能性があるためです。
また、熟練検査員は過去の経験から、通常とは異なる「違和感」を敏感に察知でき、目視検査は製品の外観品質だけでなく、製造工程全体の健全性を確認する手段としても機能します。例えば、特定の不良が増加傾向にある場合、それは設備の劣化や作業手順の逸脱を示す「危険信号」かもしれません。
安全性の確保
特に、食品・医薬品業界における製品の品質管理は、人々の健康と生命に直接影響を及ぼすため、他の製造業以上に厳格な基準と細心の注意が必要です。そのため、目視検査は、最終段階における品質保証の要として、極めて重要な役割を担っています。
食品の検査では、熟練した検査員が製品一つ一つを注意深く確認し、異物混入、変色、変形などの異常を発見し、腐敗や酸化による変色、包装材の破損なども確認します。例えば、実際の食品製造ラインでは、金属片やプラスチック片といった硬質異物から、虫や毛髪などの有機物に至るまで、あらゆる異物の混入を見逃さないよう監視が行われているのです。
また、医薬品業界においては、より一層厳格な検査基準が設けられ、錠剤やカプセルの形状異常、色むら、異物の混入に加え、PTPシートの気密性や印字の正確性まで、細部にわたる検査が必要です。
このような目視検査は、製品の安全性を確保する最後の砦として機能しています。
工程管理の改善
目視検査から得られるデータを体系的に収集・分析することで、製造工程の問題点を特定し、効果的な改善策を見出すことができます。
例えば、特定の時間帯や作業者、設備で不良品が多く発生している傾向が見られた場合、その背景にある要因を詳細に分析することで、作業手順の見直しや設備の調整、作業環境の改善などの具体的な対策を実施することが可能です。
また、不良品の発生パターンを分析することで、予防的な品質管理も可能になります。例えば、特定の原材料ロットと不良品発生率の関係性や、温度・湿度などの環境要因が品質に与える影響を把握することで、不良品の発生を未然に防ぐための管理基準を設定できます。
さらに、目視検査データの活用は、作業者の教育・訓練にも有効です。実際の不良事例をもとに、どのような点に注意して作業を行うべきか、具体的な指導が可能となります。
このように、目視検査の結果を単なる良否判定として扱うのではなく、工程改善のための重要な情報源として戦略的に活用することで、製品品質の向上と不良率の低減を実現することができます。
目視検査の種類:製品の品質を支える多様なアプローチ
目視検査は、製品の品質を確保するために欠かせない工程です。その種類は、検査の目的や製品の特性、生産環境などによって多岐にわたります。本記事では、代表的な目視検査の種類とその特徴について解説します。
1. インライン検査:生産の流れの中で行う高速検査
インライン検査は、製品が生産ライン上を流れている最中に、その場で外観検査を行う方法です。高速な検査が可能であり、生産の効率化に大きく貢献します。しかし、専用の検査設備が必要となるため、導入コストがかかるという点が挙げられます。
- 高速性: 生産ラインのスピードに合わせて、高速な検査が可能
- 効率性: 生産の流れを止めずに検査できるため、生産性の向上に繋がる
- 設備投資: 専用の検査設備が必要となるため、初期投資がかかる
2. オフライン検査:精密な検査を可能にする手法
オフライン検査は、生産ラインから製品を取り出して、専用の検査スペースでじっくりと検査を行う方法です。インライン検査では見つけにくい微細な傷や汚れなどを、より詳細に検査することができます。しかし、製品の移動に時間がかかり、生産効率が低下する可能性があります。
- 高精度: 十分な時間をかけて検査できるため、微細な不良も発見できる
- 柔軟性: さまざまな検査方法を組み合わせることが可能
- 時間とコスト: 製品移動に時間がかかり、生産効率が低下する可能性がある
3. 抜き取り検査:コストを抑えた効率的な検査
抜き取り検査は、ロットからランダムに一部の製品を選んで検査を行う方法です。全数検査に比べてコストを抑えることができ、効率的に品質を確認できます。しかし、検査対象となる製品が限られるため、全ての製品の品質を保証することはできません。
- 低コスト: 全数検査に比べてコストを抑えることができる
- 効率性: 全ての製品を検査する必要がないため、短時間で検査が完了する
- リスク: 検査対象外の製品に不良品が含まれる可能性がある
4. 全数検査:徹底した品質管理を実現する手法
全数検査は、ロットの全ての製品を対象に検査を行う方法です。最も高いレベルの品質保証を実現できますが、人件費や時間がかかるという点がデメリットです。
- 高品質: 全ての製品の品質を保証できる
- 高コスト: 人件費や時間がかかるため、コストが高くなる
目視検査を成功に導く重要なポイント
目視検査は、製品の品質を確保するための最も基本的な工程でありながら、その重要性は非常に高いです。単に「見る」という行為だけでなく、様々な要素が絡み合い、検査の精度や効率性に大きく影響を与えます。
1. 基準書の作成と徹底的な遵守
目視検査の基準書は、いわば検査の羅針盤です。この基準書がなければ、検査員一人ひとりの主観によって検査結果が異なり、製品の品質にばらつきが生じてしまいます。基準書には、検査項目、判定基準、不良品の定義などが具体的に記載され、全ての検査員が共通の目線で製品を評価できるよう設計される必要があります。
基準書を作成する際には、具体性、一貫性、そして定期的な見直しの3点を意識することが重要です。具体性とは、どの程度の傷や汚れを不良品とするか、数値や画像を用いて明確に定義することです。一貫性とは、全ての検査項目において同じ基準を適用し、判定にブレがないようにすることです。そして、定期的な見直しは、製品仕様の変更や新たな不良パターンが発生した場合に、基準書を常に最新の状態に保つために不可欠です。
2. 検査環境の最適化
検査環境は、検査員の集中力や検査精度に直接的な影響を与えます。適切な照明、色、温度、湿度、そして騒音レベルを確保することで、検査員の負担を軽減し、より正確な検査結果を得ることができます。
特に照明は、微細な傷や汚れを発見する上で非常に重要です。JIS規格の照度基準を参考に、検査対象物に最適な照明環境を構築しましょう。また、背景色や検査対象物の色とのコントラストを考慮することで、不良箇所を視覚的に際立たせることができます。温度や湿度の変化は、製品の外観や検査員の感覚に影響を与える可能性があるため、一定の環境下で検査を行うことが理想的です。
3. 検査員の育成とモチベーション維持
検査員のスキルは、検査の精度を左右する最も重要な要素の一つです。新人検査員に対しては、製品知識、検査手順、不良品の判別基準などを徹底的に教育し、経験豊富な検査員に対しても、定期的なスキルアップのための研修を実施することで、常に最新の知識を習得させましょう。
検査作業は、長時間同じ作業を繰り返す単調な作業であるため、検査員のモチベーション維持が課題となります。目標設定、フィードバック、チームワークの促進など、様々な工夫を通じて、検査員のモチベーションを高く保つことが重要です。
4. 検査時間の管理と休憩
長時間の検査は、集中力の低下や疲労によるミスにつながる可能性が高まります。適正な検査時間と休憩時間を設定し、検査員の負担を軽減することが重要です。また、作業姿勢にも注意し、定期的な休憩やストレッチを取り入れることで、身体への負担を軽減し、より長く集中力を維持できるようにしましょう。
目視での外観検査のメリット
目視検査は、製造現場において古くから行われてきた伝統的な検査手法でありながら、現代においてもその重要性を失っていません。なぜ目視検査がこれほどまでに広く活用されているのか、その理由を深く掘り下げていきましょう。
低コストで実現可能
目視検査は、特殊な設備投資を必要としない品質管理手法として、製造業界で広く活用されています。必要なのは、適切な照明設備と訓練された検査員のみであり、新製品の生産開始時や緊急時の検査体制構築にも迅速に対応可能です。
特に、多品種少量生産や頻繁な製品切り替えが必要な製造ラインでは、この柔軟性が大きな強みとなります。製品の形状や材質が変わっても、検査基準の調整や検査員への教育で対応が可能で、高額な検査設備の導入や複雑なプログラミングは不要です。
また、人間の目は複雑な判断を瞬時に行うことができ、製品表面の微妙な光沢むらや、規則性のない傷、予期せぬ異常など、定量化が困難な品質特性でも、経験豊富な検査員なら即座に良否判定を下すことができます。
柔軟性が高い
製造現場は常に変化を伴います。新しい製品の導入や製造ラインの変更など、検査環境は頻繁に変化しますが、目視検査はこうした変化に柔軟に対応することができます。人間の視覚と触覚を組み合わせることで、数値化しにくい特徴も捉えることができるため、よりきめ細やかな検査が可能です。
目視検査は、問題発生時の対応が非常に迅速です。異常を発見した場合、その場で確認し、対策を講じることができます。これにより、生産ラインの停止時間を最小限に抑え、生産効率の向上に貢献します。また、品質トラブルの拡大を防ぎ、顧客からの信頼を得る上でも重要な役割を果たします。
人間の視覚は、微妙なニュアンスやパターンを捉えることに長けています。経験豊富な検査員は、過去の経験や勘に基づいて、数値化できない不良品を見つけることができます。さらに、新しい種類の不良や、まだ定義されていない不良を発見できる可能性も秘めています。
目視による外観検査の問題
目視による外観検査の問題は大きく分けると2つに分類されます。1つ目に品質に関する問題、2つ目に生産性に関する問題です。以下ではそれぞれの問題をより細分化し、発生原因などの現象理解をしましょう。そのうえで我々はどのようにAIを活用できるかを考察していきます。
問題①:品質に関する問題
検査基準の不統一は、部署やライン間で基準が異なり、同じ製品でも異なる評価を受けるという状況を招き、製品品質の安定化を阻みます。特に、製品の複雑化や過去の慣習の影響を受けやすく、定量化が難しい特徴を持つ不良品については、主観的な評価になりがちです。また、検査基準が文書化されていなかったり、共有が不十分な場合、検査員間の認識のズレが生じ、品質にばらつきが生じます。以下が多くの発生原因です。
検査員の主観性とスキル不足は、経験や体調、スキルレベルによって検査結果が左右されることを意味します。熟練した検査員と未経験の検査員の間で、同じ不良品を見つける能力に差が生じるほか、長時間の検査作業による疲労は判断ミスにつながる可能性があります。さらに、新しい製品や検査方法への対応が遅れることで、検査員のスキル不足が問題となることもあります。以下が多くの現象原因です。
AIの導入は、目視検査の現場に革新的な変化をもたらします。従来、目視検査は検査員の経験やスキルに大きく左右されるものでした。熟練した検査員であれば、微細な傷や汚れも見逃すことなく検出できる一方で、経験の浅い検査員は、見落としや誤判定をしてしまう可能性があります。
AIは、このような検査員の経験によるばらつきを解消し、常に一定の基準で製品を評価することに長けています。AIは、大量の画像データを学習することで、製品の正常な状態と異常な状態を正確に識別するモデルを構築し、このモデルを用いることで、経験の有無に関わらず、全ての製品が同じ基準で評価されるようになります。
また、AIは24時間稼働が可能なため、長時間労働による疲労によって生じる判断ミスを防ぐことが可能です。人間の検査員は、長時間作業を行うと集中力が低下し、ミスを犯しやすくなります。しかし、AIは常に一定の性能を発揮するため、長時間稼働させても品質が低下することはありません。
さらに、AIは新しい製品の画像データを学習することで、迅速に新たな検査基準に対応することができます。従来、新しい製品の検査を開始する際には、検査員に対して新たな検査基準を教育する必要がありました。しかし、AIであれば、新しい製品の画像データを学習させるだけで、すぐに新たな検査基準に対応することができます。このように、AIは目視検査の精度向上、効率化、そして柔軟性の向上に大きく貢献するでしょう。
問題②:生産性に関する問題
検査速度の限界は、生産性の向上を阻む大きな要因の一つです。特に、複雑な製品や微細な不良を検出する必要がある場合、人間の目視検査には限界があり、検査時間が長大化してしまう傾向があります。より深く原因を探っていくと以下の点が挙げられます。
検査手順の複雑化も、生産効率の低下を招く要因です。製品の種類やバリエーションが増加し、それに伴い検査項目が細分化され、検査手順が複雑化するにつれて、ヒューマンエラーが発生しやすくなります。また、複雑な検査手順は、作業者の負担を増やし、モチベーションの低下にもつながることがあります。以下が原因として挙げられます。
長時間労働による疲労は、検査ミスの増加に直結します。長時間労働は、集中力の低下、判断力の低下、そして身体的な疲労を引き起こし、検査の精度を低下させます。さらに、単調な作業の繰り返しは、作業者の飽きやストレスを誘発し、ヒューマンエラーのリスクを高めます。
外観検査の自動化のメリット
近年、製造業において外観検査の自動化が急速に進んでいます。この背景には、製品の品質向上、生産性の向上、そしてコスト削減といった多岐にわたるメリットがあるからです。
付加価値の高い業務に人材配置できる
これまで、長時間にわたる目視での外観検査は、作業者の身体的・精神的負担となり、人材の有効活用という観点からも、製造業において大きな問題となっていました。その作業をAIが担うことで、人材をより付加価値の高い業務に配置し直すことが可能になります。
例えば、検査基準の策定や最適化、AIモデルの精度向上支援、品質改善プロセスの設計など、より戦略的な業務への移行が可能となります。これらの業務は、人間の経験や創造性が重要な役割を果たす領域であり、今のところは生成AIによる代替が難しい仕事です。単調な作業から解放されることで、従業員の満足度向上にも貢献するでしょう。
高精度かつ安定した外観検査の実現
従来の人による目視検査では、検査員の経験や主観に依存するため、検査結果にばらつきが生じやすいという問題がありました。
しかし、AIは画像認識技術を用いて、製品の傷の大きさ、色、形状といった微細な特徴を数値化し、事前に設定された基準と比較することで、高精度かつ安定した不良品判定を行えます。そのため、人間の目では見つけにくい微細な傷や汚れ、形状の変形など、様々な異常を検出することができます。特に、大量のデータを学習したAIは、新たな種類の不良品も発見できる可能性を秘めています。
また、良品と不良品の大量の画像データをAIに学習させることで、正常状態と異常状態を正確に識別するモデルを構築可能です。このモデルは人間の主観に左右されることなく一貫した判断を下し、検査基準の統一化を可能にします。さらに、AIは判断の根拠を可視化することで、検査員との基準の共有も実現可能です。
外観検査速度の向上
生成AIを用いた外観検査では、複数の画像を同時に処理することが可能です。並列処理技術により、複数カメラからの入力を瞬時に分析することで、検査速度は飛躍的に向上するでしょう。また、24時間365日の連続稼働も可能なため、人の休憩や交代が不要となり、夜間や休日も含めた長時間の安定稼働が実現できます。
加えて、検査結果のフィードバックも即時性が向上しています。不良品を検出した瞬間にアラートが発信され、自動的に結果が記録されるため、リアルタイムな情報共有による品質問題への迅速な対応が可能となるでしょう。「不良品を回収する際に生産ラインを停止する」といったタイムロスも限りなく短くすることが可能です。
属人性の排除
従来、複雑な検査手順は、詳細なマニュアルに基づいて熟練した検査員によって行われていました。しかし、AIはこれらの複雑な検査手順を自動化できます。これにより、複雑な検査マニュアルも不要になり、熟練した作業員でなくても外観検査のオペレーションを回せる様になるのです。
またAIは、新たな製品の画像データを学習することで、迅速に検査基準を更新し、多様な製品に対応することができます。従来、新しい製品の検査を開始する際には、検査員に対して新たな検査基準を教育する必要がありました。しかし、AIであれば、新しい製品の画像データを学習させるだけで、すぐに新たな検査基準に対応することができます。
まとめ:目視による外観検査の問題を自動化で解決
長年製造業の品質管理に欠かせない存在であった目視検査ですが、検査員のスキルや主観に左右されやすく、検査速度も遅いといった課題を抱えています。近年では、これらの課題を克服するため、外観検査の自動化が急速に進んできました。
AIを活用した外観検査は、画像認識技術を用いて製品の表面に現れる傷や汚れ、変形などを高精度かつ高速に検出することが可能です。これにより、人的ミスを減らし、検査品質の安定化を実現することができます。また、大量のデータを短時間で処理できるため、検査効率の大幅な向上も期待できます。
弊社は、製造業に深く根ざし、松尾研で蓄積された豊富な生成AIの知見とノウハウを活かして、製造業が抱える様々な課題に対して迅速かつ的確なAIソリューションを開発しています。生成AIは、生産性向上、コスト削減、だけでなく製品の品質向上にも貢献できるため、外観検査の自動化をご検討の方は、ぜひ無料相談をご利用ください。
株式会社エムニでは、お客様と密に連携しながら、製造業へのAI導入をサポートいたします。
エムニへの無料相談のご案内
エムニでは、製造業をはじめとする多様な業種に向けてAI導入の支援を行っており、企業様のニーズに合わせて無料相談を実施しています。
これまでに、住友電気工業株式会社、DENSO、東京ガス、太陽誘電、RESONAC、dynabook、エステー株式会社、大東建託株式会社など、さまざまな企業との取引実績があります。
AI導入の概要から具体的な導入事例、取引先の事例まで、疑問や不安をお持ちの方はぜひお気軽にご相談ください。
引用元:株式会社エムニ